Normal vector detection and posture-adjusting movement method of autonomous moving mechanism
A technology of autonomous movement and attitude adjustment, which is applied in metal processing and other directions, and can solve the problems of difficult positioning and movement of the eight-legged autonomous movement mechanism
- Summary
- Abstract
- Description
- Claims
- Application Information
AI Technical Summary
Problems solved by technology
Method used
Image
Examples
Embodiment Construction
[0078] The present invention will be further described below in conjunction with the accompanying drawings and embodiments.
[0079] As shown in Figure 1-5.
[0080] A method for normal vector detection and posture adjustment of an autonomous mobile mechanism, comprising the following steps:
[0081] First, three or four laser ranging sensors are installed on the end effector of the autonomous mobile mechanism;
[0082] Secondly, use the values measured by three or four laser ranging sensors to obtain the measured hole plane normal vector n;
[0083] Third, according to the normal vector n of the hole-making plane obtained from the above-mentioned measurement and calculation, the driving force of each leg of the autonomous moving mechanism to the normal vector of hole-making is obtained through the inverse solution algorithm of the attitude-adjusting motion, which is used for the control system to realize the attitude-adjusting motion;
[0084] Finally, according to the ab...
PUM
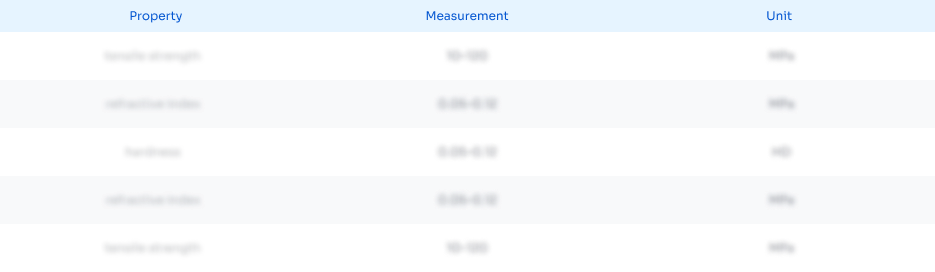
Abstract
Description
Claims
Application Information

- R&D
- Intellectual Property
- Life Sciences
- Materials
- Tech Scout
- Unparalleled Data Quality
- Higher Quality Content
- 60% Fewer Hallucinations
Browse by: Latest US Patents, China's latest patents, Technical Efficacy Thesaurus, Application Domain, Technology Topic, Popular Technical Reports.
© 2025 PatSnap. All rights reserved.Legal|Privacy policy|Modern Slavery Act Transparency Statement|Sitemap|About US| Contact US: help@patsnap.com