Tool replacing device for tail end of space robot
A space robot and tool replacement technology, which is applied in the direction of tools, manufacturing tools, manipulators, etc., can solve the problems of not being able to lock the docking parts, not being able to realize the large tolerance capture of replacement tools and standard interfaces, and not being able to realize power output, etc., to achieve The effect of installation and maintenance
- Summary
- Abstract
- Description
- Claims
- Application Information
AI Technical Summary
Problems solved by technology
Method used
Image
Examples
specific Embodiment approach 1
[0015] Specific implementation mode one: combine Figure 1-Figure 6 Describe this embodiment, a tool replacement device for the end of a space robot in this embodiment includes a base A1, a connecting sleeve A2, a capture locking and electrical pushing system B and a drive mechanism C; the base A1 is equipped with a connecting sleeve A2;
[0016] The capture locking and electrical appliance pushing system B includes an interface sleeve B1, a docking sleeve B2, a first motor B5, a first harmonic drive reducer B7, a rotating body B11, three sets of capture claws B12, three sets of contact switches B14 and Three sets of electrical relay mechanism B15;
[0017] The lower end surface of the interface sleeve B1 is connected with the connection sleeve A2, and the upper end surface of the interface sleeve B1 is connected with the docking sleeve B2; the connection sleeve A2 is provided with the first motor B5, and the interface sleeve B1 is provided with the first harmonic drive reduce...
specific Embodiment approach 2
[0025] Specific implementation mode two: combination figure 1 with figure 2 To describe this embodiment, the connecting sleeve A2 in this embodiment is a cylindrical connecting sleeve. Such setting is convenient to use and meets design requirements and actual needs. Others are the same as in the first embodiment.
specific Embodiment approach 3
[0026] Specific implementation mode three: combination figure 2 To illustrate this embodiment, the interface sleeve B1 in this embodiment is a tapered cylindrical interface sleeve, the butt joint sleeve B2 is a cylindrical butt joint sleeve, the small diameter end of the interface sleeve B1 is connected to the connection sleeve A2, and the large diameter end of the interface sleeve B1 The diameter end is connected with the butt sleeve B2. Such setting is convenient to use and meets design requirements and actual needs. Others are the same as in the second embodiment.
PUM
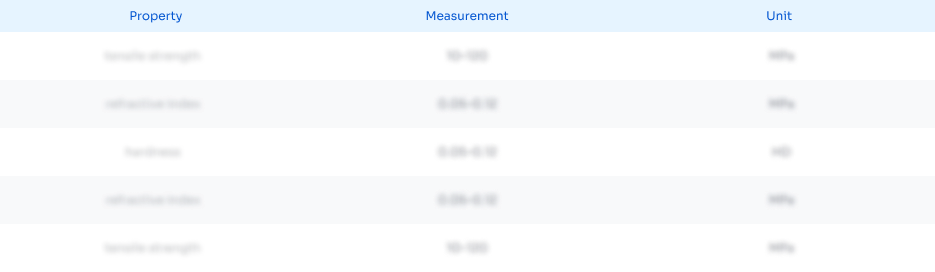
Abstract
Description
Claims
Application Information

- R&D
- Intellectual Property
- Life Sciences
- Materials
- Tech Scout
- Unparalleled Data Quality
- Higher Quality Content
- 60% Fewer Hallucinations
Browse by: Latest US Patents, China's latest patents, Technical Efficacy Thesaurus, Application Domain, Technology Topic, Popular Technical Reports.
© 2025 PatSnap. All rights reserved.Legal|Privacy policy|Modern Slavery Act Transparency Statement|Sitemap|About US| Contact US: help@patsnap.com