Unified model of catadioptric omnidirectional camera and calibration method thereof
A catadioptric and camera technology, applied in image data processing, instruments, computing, etc., can solve problems such as complex imaging models, tangential distortions that cannot be compensated, and unsatisfactory calibration results
- Summary
- Abstract
- Description
- Claims
- Application Information
AI Technical Summary
Problems solved by technology
Method used
Image
Examples
Embodiment
[0083] Catadioptric camera consists of H3S hyperbolic mirror (a=0.0281m, b=0.0234m) and SONYXCD-SX910CR camera (f x =1455, f y =1459,α=0,u 0 =639.2, v 0 =482.2, resolution 1280×960). The catadioptric camera collects 20 checkerboard images with a grid number of 7×10 (the number of intersection points is 6×9).
[0084] Select the mirror edge in the image, and calculate the center of the mirror edge as (u 0 ,v 0 ) initial value (u 0 =615.7, v 0 =443.9), select four points on the same line in the image to calculate the initial value of γ=374.5. At this point, the initial values of the internal parameters of the model have been obtained.
PUM
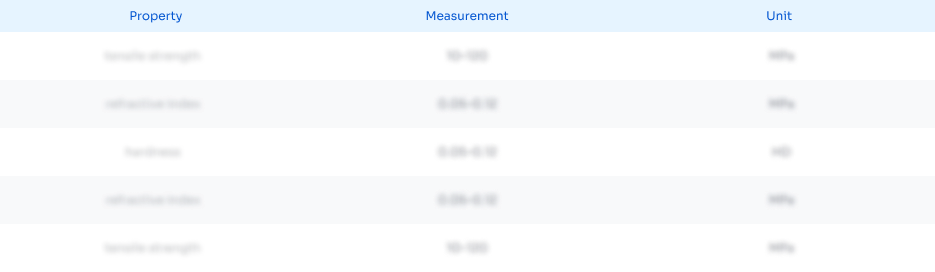
Abstract
Description
Claims
Application Information

- Generate Ideas
- Intellectual Property
- Life Sciences
- Materials
- Tech Scout
- Unparalleled Data Quality
- Higher Quality Content
- 60% Fewer Hallucinations
Browse by: Latest US Patents, China's latest patents, Technical Efficacy Thesaurus, Application Domain, Technology Topic, Popular Technical Reports.
© 2025 PatSnap. All rights reserved.Legal|Privacy policy|Modern Slavery Act Transparency Statement|Sitemap|About US| Contact US: help@patsnap.com