Automotive rear bulkhead fabric laminating lifting mechanism
A lifting mechanism and rear partition technology, applied in the direction of lifting frame, lifting device, etc., can solve the problems of high material production cost, complex structure, and large inertial force up and down the conveying mechanism, so as to reduce the labor intensity of workers, improve the quality of products, The effect of a high degree of automation
- Summary
- Abstract
- Description
- Claims
- Application Information
AI Technical Summary
Problems solved by technology
Method used
Image
Examples
Embodiment Construction
[0017] The present invention will be further described below in conjunction with specific drawings and embodiments.
[0018] like figure 1 As shown: the automobile rear bulkhead fabric bonding lifting mechanism in the embodiment mainly includes a base 1, a frame, a slide rail slider assembly, a lifting frame, a cylinder 12 and a fixing seat 16, and the frame is vertically installed on the rear of the base 1 The slide rail 6 in the slide rail slider assembly is installed on the main columns 3 on both sides of the frame, the lifting frame is arranged in the frame, and the lifting frame is connected with the slider 5 in the slide rail slider assembly The cylinder 12 is vertically arranged, the lower end of the cylinder 12 is connected to the base 1, and the upper end of the cylinder 12 is upwardly connected to the lifting frame, and the fixed seat 16 for connecting the fabric delivery platform 18 is installed on the lifting frame.
[0019] like figure 1 As shown, in the embod...
PUM
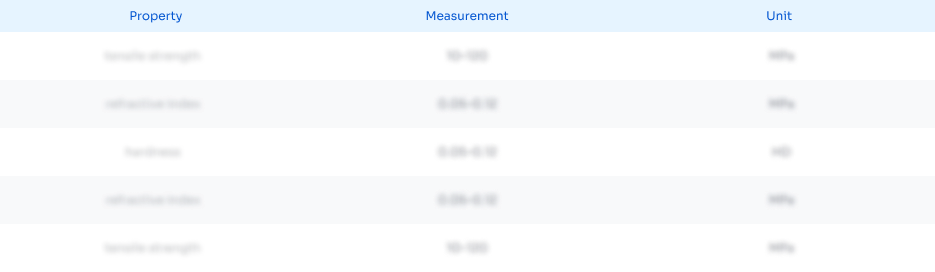
Abstract
Description
Claims
Application Information

- R&D
- Intellectual Property
- Life Sciences
- Materials
- Tech Scout
- Unparalleled Data Quality
- Higher Quality Content
- 60% Fewer Hallucinations
Browse by: Latest US Patents, China's latest patents, Technical Efficacy Thesaurus, Application Domain, Technology Topic, Popular Technical Reports.
© 2025 PatSnap. All rights reserved.Legal|Privacy policy|Modern Slavery Act Transparency Statement|Sitemap|About US| Contact US: help@patsnap.com