Wafer prealignment device
A pre-alignment and wafer technology, applied in electrical components, semiconductor/solid-state device manufacturing, circuits, etc., can solve problems such as tilt, uneven force, and inability to clamp wafers
- Summary
- Abstract
- Description
- Claims
- Application Information
AI Technical Summary
Problems solved by technology
Method used
Image
Examples
Embodiment Construction
[0028] The above-mentioned wafer pre-alignment device will be further described below through specific embodiments and accompanying drawings.
[0029] Please also see figure 1 , figure 2 and Figure 5 , a wafer pre-alignment device 100 according to one embodiment includes a substrate 10, a first supporting device 20, a second supporting device 30, a first driving device 40, a second driving device 50, a sensor 60, and a control unit (not shown in the figure) ), bearing 70 and protection box 80.
[0030] The substrate 10 is substantially a rectangular plate, and a first through hole 12 and a plurality of second through holes 14 are opened on the substrate 10 . The first through hole 12 is opened in the middle of the substrate 10 , and the second through hole 14 is located around the first through hole 12 . In this embodiment, the number of the second through holes 14 is four.
[0031] see image 3 , the first support device 20 includes a support base 22 , a connector 24 ...
PUM
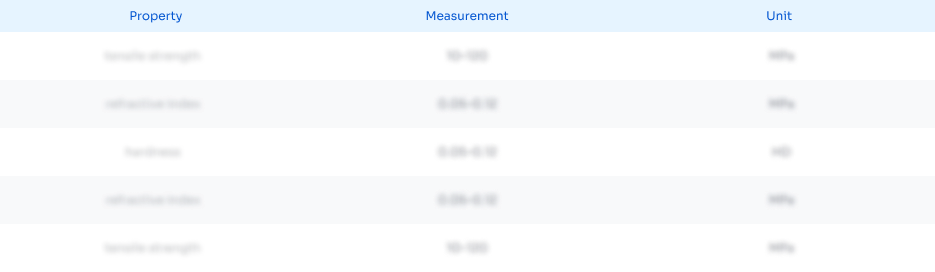
Abstract
Description
Claims
Application Information

- R&D
- Intellectual Property
- Life Sciences
- Materials
- Tech Scout
- Unparalleled Data Quality
- Higher Quality Content
- 60% Fewer Hallucinations
Browse by: Latest US Patents, China's latest patents, Technical Efficacy Thesaurus, Application Domain, Technology Topic, Popular Technical Reports.
© 2025 PatSnap. All rights reserved.Legal|Privacy policy|Modern Slavery Act Transparency Statement|Sitemap|About US| Contact US: help@patsnap.com