Double-circle method for generating trailing edge flap control surface airfoil leading edge curve
A technology of trailing edge flaps and leading edges, which is applied in the field of double-circle method to generate trailing edge flap rudder surface airfoil leading edge curves, which can solve problems such as poor operability, cumbersome operation, and poor curve quality
- Summary
- Abstract
- Description
- Claims
- Application Information
AI Technical Summary
Problems solved by technology
Method used
Image
Examples
Embodiment
[0025] Example: see Figure 4 , Figure 5 .
[0026] A kind of double-circle method that generates trailing edge flap rudder surface airfoil leading edge curve, is characterized in that, comprises the steps:
[0027] In the first step, two points c1 and c6 intersecting the aircraft wing in the leading edge curve and a known chord length control point c2 are retained, wherein point c2 is given by aerodynamic technicians and is known in the prior art;
[0028] The second step is to select the control point c7 at the highest point of the maximum thickness of the leading edge of the aircraft;
[0029] The third step is to smoothly fit the above four points in sequence, and use the first curvature circle 3 and the second curvature circle 4 to control the curvatures at points c2 and c7 respectively to obtain a smooth curve.
[0030] The first curvature circle 3 and the second curvature circle 4 pass through point c2 and point c7 respectively, and the radii of the first curvature ...
PUM
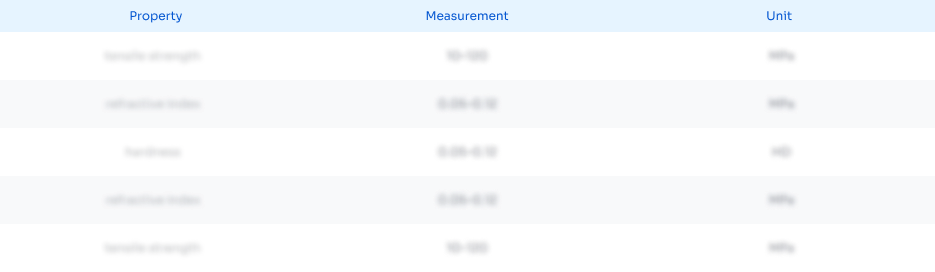
Abstract
Description
Claims
Application Information

- R&D Engineer
- R&D Manager
- IP Professional
- Industry Leading Data Capabilities
- Powerful AI technology
- Patent DNA Extraction
Browse by: Latest US Patents, China's latest patents, Technical Efficacy Thesaurus, Application Domain, Technology Topic, Popular Technical Reports.
© 2024 PatSnap. All rights reserved.Legal|Privacy policy|Modern Slavery Act Transparency Statement|Sitemap|About US| Contact US: help@patsnap.com