Transparent shoe sole and making method thereof
A transparent and oil-operating technology, applied in the field of shoe production, can solve the problems of insufficient sole properties, inability to meet the physical properties of rubber materials and production standards, cost control, etc., and achieve the effects of low defective products, easy operation and lower production costs.
- Summary
- Abstract
- Description
- Claims
- Application Information
AI Technical Summary
Problems solved by technology
Method used
Examples
Embodiment 1
[0022] The transparent sole of the present invention is composed of the following components by mass: 30 parts of butadiene rubber; 10 parts of isoprene rubber IR307; 10 parts of styrene butadiene rubber SSBR303; 30 parts of superfine white carbon black; 15 parts of operating oil; Acid 0.5 part; antioxidant β-(3,5-di-tert-butyl-4-hydroxyphenyl) n-octadecyl propionate 1 part; coupling agent bis-(3-triethoxysilane propyl )-1 part of tetrasulfide; 3 parts of bridging agent di-sec-octyl phthalate;
Embodiment 2
[0024] The transparent sole of the present invention is composed of the following components by mass: 35 parts of butadiene rubber; 8 parts of isoprene rubber IR307; 15 parts of styrene butadiene rubber SSBR303; 35 parts of superfine silica; 18 parts of operating oil; Acid 0.3 parts; antioxidant β-(3,5-di-tert-butyl-4-hydroxyphenyl) n-octadecyl propionate 1 part; coupling agent bis-(3-triethoxysilane propyl )-1 part of tetrasulfide; 2 parts of bridging agent di-sec-octyl phthalate;
Embodiment 3
[0026] The transparent sole of the present invention is composed of the following components by mass: 40 parts of butadiene rubber; 6 parts of isoprene rubber IR307; 20 parts of styrene butadiene rubber SSBR1205; 40 parts of ultrafine white carbon black; 20 parts of operating oil; Acid 0.2 parts; antioxidant β-(3,5-di-tert-butyl-4-hydroxyphenyl) propionic acid n-octadecyl alcohol ester 2 parts; coupling agent bis-(3-triethoxysilane propyl )-1.5 parts of tetrasulfide; 2.5 parts of bridging agent di-sec-octyl phthalate;
PUM
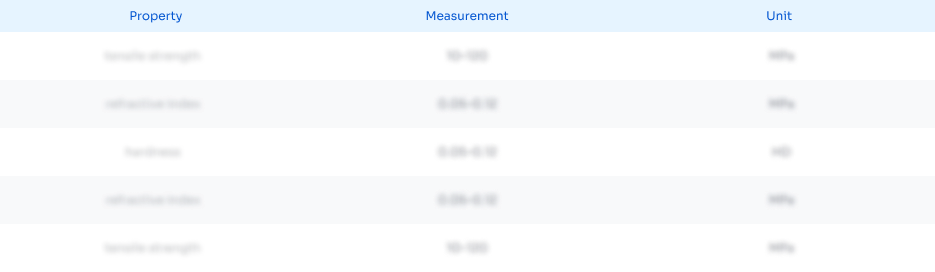
Abstract
Description
Claims
Application Information

- R&D Engineer
- R&D Manager
- IP Professional
- Industry Leading Data Capabilities
- Powerful AI technology
- Patent DNA Extraction
Browse by: Latest US Patents, China's latest patents, Technical Efficacy Thesaurus, Application Domain, Technology Topic, Popular Technical Reports.
© 2024 PatSnap. All rights reserved.Legal|Privacy policy|Modern Slavery Act Transparency Statement|Sitemap|About US| Contact US: help@patsnap.com