Foaming mold for manufacturing PU (polyurethane) automobile back cushion
A technology of foaming molds and cushions, which is applied in the field of foaming molds for manufacturing PU automobile cushions. It can solve problems such as affecting quality, poor exhaust effect at the top, and inconvenient product removal, so as to improve safety and reliability and reduce possibilities. Effect
- Summary
- Abstract
- Description
- Claims
- Application Information
AI Technical Summary
Problems solved by technology
Method used
Image
Examples
Embodiment Construction
[0016] Such as figure 1 , 2 Shown, comprise upper mold frame 1, lower mold frame 2, mold opening chain 3, upper mold 4, lower mold 5, middle block 6, separation driving mechanism 7, locking cylinder 81, locking shaft 82, detector 83.
[0017] The ends of the above-mentioned upper mold base 1 and lower mold base 2 are hinged (not shown in the figure), the two sides of the lower mold base 2 are equipped with a mold base turning cylinder, and the piston rod of the mold base turning cylinder is connected to the two sides of the upper mold base. Hinged midside. The front ends of the upper mold base 1 and the lower mold base 2 are provided with mechanisms for locking the upper and lower mold bases, and the mold base structures all adopt commonly used known structures, which will not be repeated here.
[0018] Mold comprises upper die 4, lower die 5 and middle block 6, the ends of upper die 4 and lower die 5 are hinged, lower die 5 is fixed on lower die frame 2, middle block 6 is a...
PUM
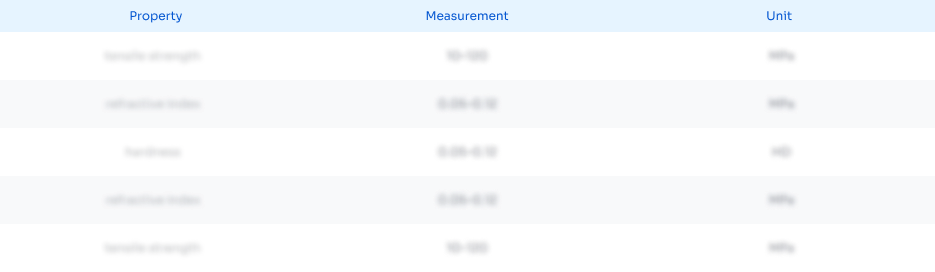
Abstract
Description
Claims
Application Information

- Generate Ideas
- Intellectual Property
- Life Sciences
- Materials
- Tech Scout
- Unparalleled Data Quality
- Higher Quality Content
- 60% Fewer Hallucinations
Browse by: Latest US Patents, China's latest patents, Technical Efficacy Thesaurus, Application Domain, Technology Topic, Popular Technical Reports.
© 2025 PatSnap. All rights reserved.Legal|Privacy policy|Modern Slavery Act Transparency Statement|Sitemap|About US| Contact US: help@patsnap.com