Earpiece moulding method by implanting plastic into metal fittings
A metal fitting and forming method technology, applied in the field of glasses, can solve the problems such as the radian and curvature of metal fittings cannot be adjusted arbitrarily, the forming method of glasses legs is time-consuming, and the quality of products is unstable, so as to achieve diversification of product types, save forming time, Easy-to-shape effect
- Summary
- Abstract
- Description
- Claims
- Application Information
AI Technical Summary
Problems solved by technology
Method used
Image
Examples
Embodiment Construction
[0050] Please refer to Figure 4 to Figure 10 Shown, it has shown the molding process of preferred embodiment of the present invention, comprises the following steps:
[0051] (1) Put the metal fitting 20 in the mold cavity 100 of the mold, the mold includes a lower mold 101 and an upper mold 101 , and the mold cavity 100 is formed by the upper mold 102 and the lower mold 101 .
[0052] (2) The thimble 30 is set on the mold, and the thimble 30 extends into the mold cavity 100 to hold up the metal fitting 20 so that the metal fitting 20 is suspended and fixed in the mold cavity 100; specifically, in this embodiment, as Figure 4 As shown, the front and rear ends of the mold are equipped with thimbles 30, and the thimbles 30 extend into the mold cavity 100 to hold up the metal fitting 20 so that the metal fitting 20 is suspended and fixed in the mold cavity 100; Each group of thimbles 30 includes an upper thimble 31 and a lower thimble 32. The upper thimble 31 extends from the ...
PUM
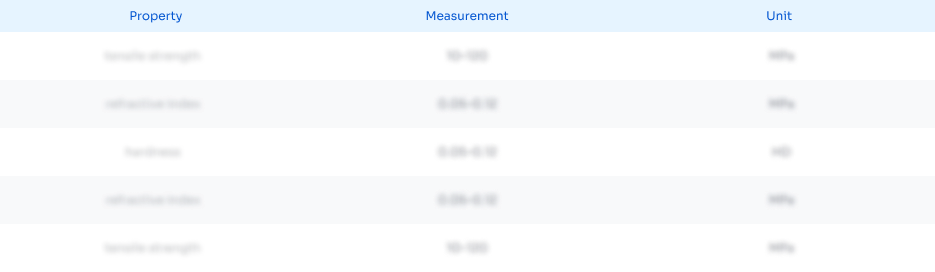
Abstract
Description
Claims
Application Information

- R&D
- Intellectual Property
- Life Sciences
- Materials
- Tech Scout
- Unparalleled Data Quality
- Higher Quality Content
- 60% Fewer Hallucinations
Browse by: Latest US Patents, China's latest patents, Technical Efficacy Thesaurus, Application Domain, Technology Topic, Popular Technical Reports.
© 2025 PatSnap. All rights reserved.Legal|Privacy policy|Modern Slavery Act Transparency Statement|Sitemap|About US| Contact US: help@patsnap.com