Liquid die forging and rolling compound formation method for stainless steel irregular-section large ring piece
A liquid die forging and rolling composite technology, applied in metal rolling and other directions, can solve the problems of low utilization rate of materials, many processes, and lengthy processes, so as to improve productivity and economic benefits, improve comprehensive mechanical properties, and be widely popularized and applied. Foreground effect
- Summary
- Abstract
- Description
- Claims
- Application Information
AI Technical Summary
Problems solved by technology
Method used
Examples
no. 1 example
[0033] The liquid die forging and rolling compound forming method for stainless steel large rings with different cross-sections in this embodiment includes smelting→liquid die forging→homogenization→waste heat isothermal rolling→heat treatment→finishing. The stainless steel in this embodiment is 0Cr17Ni12Mo2.
[0034] The smelting process is as follows: the stainless steel is smelted in a melting furnace, and after the smelting of the stainless steel is completed, the stainless steel solution is refined outside the ladle refining furnace, and the temperature of the external refining in this embodiment is 1600°C.
[0035] Liquid die forging is as follows: after fixing the liquid die forging die on the indirect squeeze casting machine, quantitatively pour the molten stainless steel solution into the liquid die forging die at a pouring temperature of 1550 °C and a pressurization speed of 30 mm / s. The filling time is 6 s, the specific pressure is 150 MPa, and the pressure is mainta...
no. 2 example
[0053] The liquid die forging and rolling compound forming method for large stainless steel rings with different cross-sections in this embodiment includes smelting→liquid die forging→homogenization→waste heat isothermal rolling→heat treatment→finishing. The stainless steel in this embodiment is 0Cr18Ni9Ti.
[0054] The smelting process is as follows: the stainless steel is smelted in the melting furnace, and after the smelting of the stainless steel is completed, the stainless steel solution is refined outside the ladle refining furnace, and the temperature of the external refining in this embodiment is 1650°C.
[0055] Liquid die forging is as follows: after fixing the liquid die forging die on the indirect squeeze casting machine, the stainless steel solution obtained after smelting is quantitatively poured into the liquid die forging die. The molding time is 1 s, the specific pressure is 200 MPa, and the pressure is maintained at this pressure for 35 s to obtain a ring blan...
no. 3 example
[0073] The liquid die forging and rolling compound forming method for large stainless steel rings with different cross-sections in this embodiment includes smelting→liquid die forging→homogenization→waste heat isothermal rolling→heat treatment→finishing. The stainless steel in this embodiment is 0Cr19Ni9.
[0074] The smelting process is as follows: the stainless steel is smelted in a melting furnace. After the stainless steel smelting is completed, the stainless steel solution is refined outside the ladle refining furnace, and the temperature of the external refining in this embodiment is 1620°C.
[0075] Liquid die forging is as follows: after fixing the liquid die forging die on the indirect squeeze casting machine, the stainless steel solution obtained after smelting is quantitatively poured into the liquid die forging die, the pouring temperature is 1580°C, the pressurization speed is 35mm / s, and the filling The molding time is 5 s, the specific pressure is 180 MPa, and th...
PUM
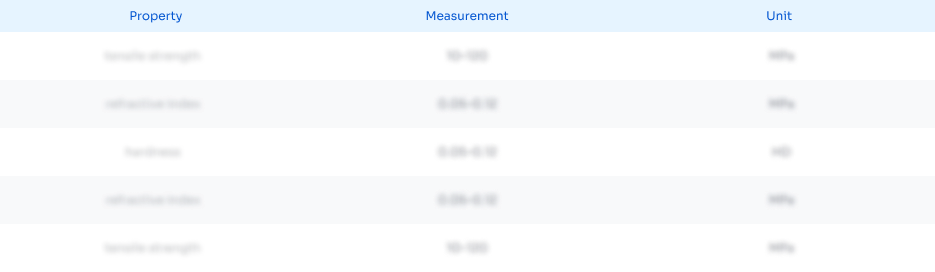
Abstract
Description
Claims
Application Information

- Generate Ideas
- Intellectual Property
- Life Sciences
- Materials
- Tech Scout
- Unparalleled Data Quality
- Higher Quality Content
- 60% Fewer Hallucinations
Browse by: Latest US Patents, China's latest patents, Technical Efficacy Thesaurus, Application Domain, Technology Topic, Popular Technical Reports.
© 2025 PatSnap. All rights reserved.Legal|Privacy policy|Modern Slavery Act Transparency Statement|Sitemap|About US| Contact US: help@patsnap.com