Surrogate patch for composite repair process
A patch and composite structure technology, applied in the application of thermometers, material analysis through electromagnetic means, instruments, etc., can solve problems such as time-consuming, expensive materials, and labor-intensive
- Summary
- Abstract
- Description
- Claims
- Application Information
AI Technical Summary
Problems solved by technology
Method used
Image
Examples
Embodiment Construction
[0115] Referring now to the accompanying drawings, wherein the drawings are only for illustration of preferred and different embodiments of the present invention and are not intended to limit the embodiments, figure 1 Shown is a perspective view of composite structure 10, and can be used as Figure 4-9 The surrogate patch assembly implements the repair process on the composite structure 10 . More specifically, preparing the rework area 20 may include a thermal survey and / or moisture removal process, which may employ a surrogate patch assembly 50 as described herein and made from low cost materials in a relatively short period of time ( Figure 4-9 ), which will be described in more detail below.
[0116] exist Figure 1-2 In this example, a composite structure 10 may include a skin 14 formed from plies 12 of composite material, where the skin 14 may have an upper surface 16 and a lower surface 18 . Composite structure 10 may include a reworked area 20 formed within skin 14 ...
PUM
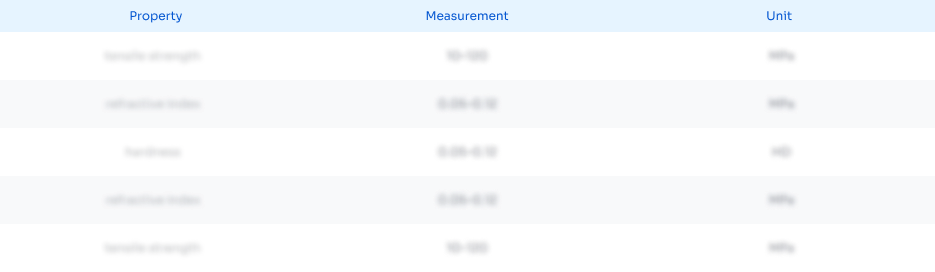
Abstract
Description
Claims
Application Information

- R&D
- Intellectual Property
- Life Sciences
- Materials
- Tech Scout
- Unparalleled Data Quality
- Higher Quality Content
- 60% Fewer Hallucinations
Browse by: Latest US Patents, China's latest patents, Technical Efficacy Thesaurus, Application Domain, Technology Topic, Popular Technical Reports.
© 2025 PatSnap. All rights reserved.Legal|Privacy policy|Modern Slavery Act Transparency Statement|Sitemap|About US| Contact US: help@patsnap.com