Five-axis side milling cutting force predicting method based on ACIS platform
A cutting force prediction and milling technology, applied in special data processing applications, instruments, electrical digital data processing, etc., can solve problems such as not reflecting processing conditions
- Summary
- Abstract
- Description
- Claims
- Application Information
AI Technical Summary
Problems solved by technology
Method used
Image
Examples
Embodiment Construction
[0034] The embodiments of the present invention are described in detail below: the present embodiment is implemented under the premise of the technical solution of the present invention, and detailed implementation and specific operation process are provided, but the protection scope of the present invention is not limited to the following implementation example. The process flow of the five-axis CNC side milling cutting force prediction method proposed by the present invention is as follows figure 1 shown.
[0035] In this embodiment, 1 is the tool axis, 2 is the handle, 3 is the tool, 4 is the cutting edge, 5 is the tool reference point, 6 is the spindle axis, 7 is the actual tool reference point, 8 is the tool position point, dF r,i,j is the unit radial cutting force of the i-th blade on the j-th disc, dF t,j,k is the unit tangential cutting force of the i-th blade on the j-th disc, dF a,j,k is the unit axial cutting force of the i-th blade on the j-th disc. {O r ;X r...
PUM
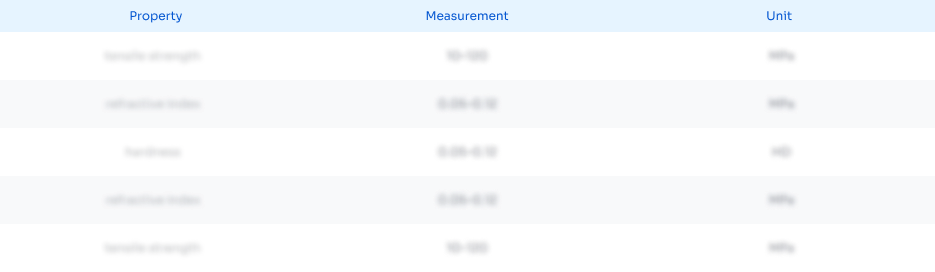
Abstract
Description
Claims
Application Information

- R&D
- Intellectual Property
- Life Sciences
- Materials
- Tech Scout
- Unparalleled Data Quality
- Higher Quality Content
- 60% Fewer Hallucinations
Browse by: Latest US Patents, China's latest patents, Technical Efficacy Thesaurus, Application Domain, Technology Topic, Popular Technical Reports.
© 2025 PatSnap. All rights reserved.Legal|Privacy policy|Modern Slavery Act Transparency Statement|Sitemap|About US| Contact US: help@patsnap.com