Construction method of car steel plate spring multi-body model
A leaf spring, multi-body model technology, applied in special data processing applications, instruments, electrical digital data processing, etc., can solve problems such as difficult calculation, complex modeling, and tedious modeling process, and achieve accurate ride comfort simulation.
- Summary
- Abstract
- Description
- Claims
- Application Information
AI Technical Summary
Problems solved by technology
Method used
Image
Examples
Embodiment Construction
[0041] The present invention will be described in detail below in conjunction with the embodiments and the accompanying drawings.
[0042] For the specific operation steps and the output results of each step of the construction method of a kind of automobile leaf spring multi-body model described in the present invention, please refer to figure 1 , including the following steps:
[0043] The first step is to test the static stiffness and dynamic force of the leaf spring;
[0044] see figure 2 , support the leaf spring 6 on the guide rail 8 through the support 7, manipulate the static actuator 5 to slowly load, record the load and the deformation of the leaf spring, and test the static stiffness of the leaf spring;
[0045] Load the leaf spring to the design load, and it is in static balance; press 1-15mm, 1-2Hz sine wave to load, and record the deformation and force of the leaf spring;
[0046] The second step is to establish a dynamic friction model;
[0047] Model param...
PUM
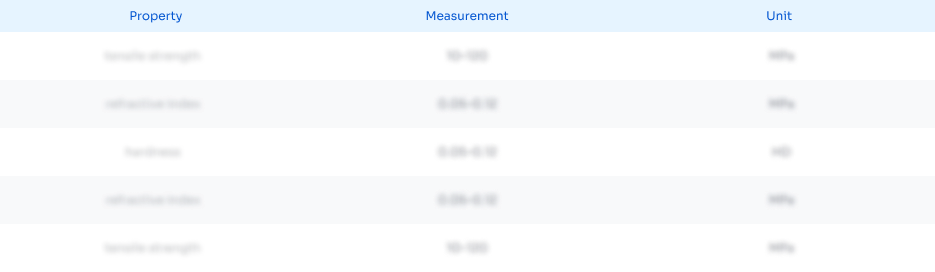
Abstract
Description
Claims
Application Information

- R&D
- Intellectual Property
- Life Sciences
- Materials
- Tech Scout
- Unparalleled Data Quality
- Higher Quality Content
- 60% Fewer Hallucinations
Browse by: Latest US Patents, China's latest patents, Technical Efficacy Thesaurus, Application Domain, Technology Topic, Popular Technical Reports.
© 2025 PatSnap. All rights reserved.Legal|Privacy policy|Modern Slavery Act Transparency Statement|Sitemap|About US| Contact US: help@patsnap.com