Combined stacked carbonization furnace
A carbonization furnace and carbonization technology, applied in fixed carbonization furnaces, coke ovens, special forms of dry distillation, etc., can solve the problems of low efficiency and achieve the effects of saving energy, saving production costs and high efficiency
- Summary
- Abstract
- Description
- Claims
- Application Information
AI Technical Summary
Problems solved by technology
Method used
Image
Examples
Embodiment 1
[0027] The combined stacked carbonization furnace includes ten carbonization units, and the carbonization units sequentially include a stacking chamber 1, a carbonization chamber 2, and a cooling chamber 3 that are connected to each other along the process flow; adjacent chambers can be connected or sealed. Every two carbonization units form a group, and a recovery chamber 4 is set between the two carbonization units in each group; a heating chamber is arranged inside the stacking chamber 1, and five layers of mutually sealed material boxes are placed in the heating chamber from top to bottom 5. The uppermost material box 5 is provided with a sealed box cover 51; the lower part of the heating chamber is provided with a one-way bayonet 13 for carrying the material box 5, and the side wall of the material box 5 is provided with a through hole 52, and the side wall of the heating chamber A heat conduction channel 14 is provided, and a heat conduction tube that can freely move up a...
PUM
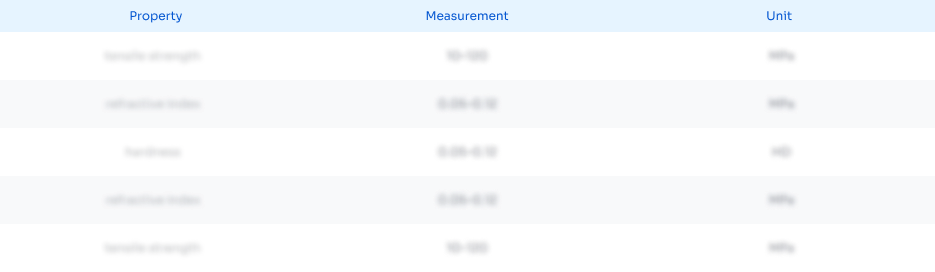
Abstract
Description
Claims
Application Information

- R&D
- Intellectual Property
- Life Sciences
- Materials
- Tech Scout
- Unparalleled Data Quality
- Higher Quality Content
- 60% Fewer Hallucinations
Browse by: Latest US Patents, China's latest patents, Technical Efficacy Thesaurus, Application Domain, Technology Topic, Popular Technical Reports.
© 2025 PatSnap. All rights reserved.Legal|Privacy policy|Modern Slavery Act Transparency Statement|Sitemap|About US| Contact US: help@patsnap.com