Compliant joint taking irregular plate spring with variable cross section as skeleton
A leaf spring and skeleton technology, applied in the field of leaf spring skeleton compliant joints, can solve problems such as the need to improve the dynamic response, the need to improve the dynamic response, and the uneven force of the leaf spring, so as to facilitate the analysis and calculation, improve the dynamic response, Avoid contact interference effects
- Summary
- Abstract
- Description
- Claims
- Application Information
AI Technical Summary
Problems solved by technology
Method used
Image
Examples
Embodiment Construction
[0037] Below the present invention is combined with attached Figure 14 The first implementation of the scheme is further described:
[0038]In Scheme 1, the two ends of the elastic bellows 10 are fixed on the pipe joint 8 through the pressure piece 9, and the pipe joints 8 at both ends of the bellows are respectively connected with the headstock 5 and the tailstock 11, and are locked by the lock nut 7, with a Gasket 6 is sealed to form a gas cavity. There is an air inlet on the tailstock 11, and the air inlet pipe joint 13 is fixed on the tailstock 11 through the sealing ring 12. The headstock 5 and the tailstock 11 are respectively fixed with the head section 1 and the tail section 14 through the adjustment cushion block 4 . There are positioning pins on the upper and lower surfaces of the adjustment cushion block 4 to ensure the mutual positioning between the headstock 5 and the head section 1 as well as the tailstock 11 and the tail section 14. The two ends of the trape...
PUM
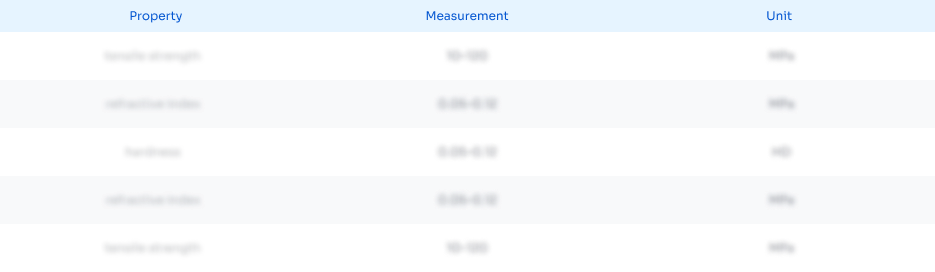
Abstract
Description
Claims
Application Information

- R&D
- Intellectual Property
- Life Sciences
- Materials
- Tech Scout
- Unparalleled Data Quality
- Higher Quality Content
- 60% Fewer Hallucinations
Browse by: Latest US Patents, China's latest patents, Technical Efficacy Thesaurus, Application Domain, Technology Topic, Popular Technical Reports.
© 2025 PatSnap. All rights reserved.Legal|Privacy policy|Modern Slavery Act Transparency Statement|Sitemap|About US| Contact US: help@patsnap.com