Acid-alkali in situ preparation method of lead-free rare earth/ rubber composite shielding material
A compound shielding and in-situ preparation technology, which is applied in radiation safety devices and other directions, can solve problems such as cracks, reduced mechanical properties, and rapid aging
- Summary
- Abstract
- Description
- Claims
- Application Information
AI Technical Summary
Problems solved by technology
Method used
Image
Examples
Embodiment 1
[0025] The composition and weight fraction of each component are:
[0026] Nitrile rubber 100
[0027] Samarium Hydroxide 30
[0028] Methacrylic acid 40
[0029] 2,5-Dimethyl-2,5-bis(tert-butylperoxy)hexane 3
[0030] At room temperature, put 100 parts of nitrile rubber on the open mill to masticate thin pass for 2 minutes, then add 30 parts of samarium hydroxide to the roller, and mix for 3 minutes; turn on the cooling water switch, and maintain the temperature of the roller at 60°C. Start to add 40 parts of methacrylic acid dropwise and mix for 6 minutes; finally add 3 parts of 2,5-dimethyl-2,5-bis(tert-butylperoxy)hexane, make 6 triangular bags, After the rollers were parked for 24 hours, they were vulcanized and molded on a flat plate at 170°C to obtain a composite material.
Embodiment 2
[0032] The composition and weight fraction of each component are:
[0033] Nitrile rubber 100
[0034] Samarium Hydroxide 130
[0035] Gadolinium Hydroxide 130
[0036] Methacrylic acid 340
[0037] 2,5-Dimethyl-2,5-bis(tert-butylperoxy)hexane 5
[0038] At normal temperature, put 100 parts of nitrile rubber on the open mill to masticate the thin pass for 2 minutes, then add 130 parts of samarium hydroxide and 130 parts of gadolinium hydroxide to the roller successively, and knead for 15 minutes; Turn on the switch, and when the roller temperature is maintained at 80°C, start to add 340 parts of methacrylic acid dropwise and mix for 20 minutes; finally add 5 parts of 2,5-dimethyl-2,5-bis(tert-butyl peroxy ) hexane, bagged 8 times, and after the lower roll was parked for 24 hours, it was vulcanized and molded on a flat plate at 170°C to obtain a composite material.
Embodiment 3
[0040]The composition and weight fraction of each component are:
[0041] Nitrile rubber 100
[0042] Samarium Hydroxide 90
[0043] Gadolinium Hydroxide 100
[0044] Dysprosium hydroxide 90
[0045] Methacrylic acid 380
[0046] Dicumyl peroxide 6
[0047] At normal temperature, put 100 parts of nitrile rubber on the open mill to masticate the thin pass for 2 minutes, then add 90 parts of samarium hydroxide, 100 parts of gadolinium hydroxide and 90 parts of dysprosium hydroxide to the roller successively, and knead 15 minutes; turn on the cooling water switch, wait until the roller temperature is maintained at 80°C, start to add 380 parts of methacrylic acid dropwise, and mix for 20 minutes; finally add 6 parts of dicumyl peroxide, make 8 triangle bags, After the rollers were parked for 24 hours, they were vulcanized and molded on a flat plate at 160°C to obtain a composite material.
PUM
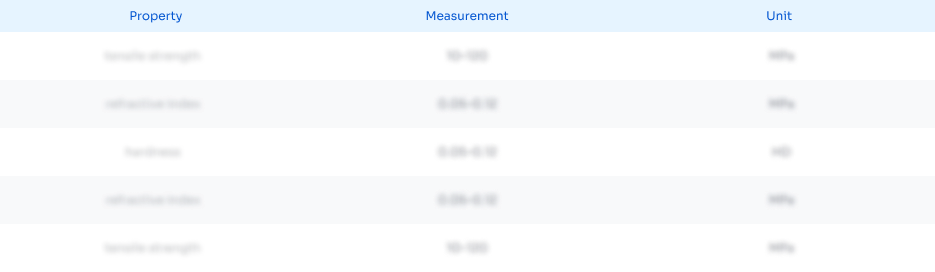
Abstract
Description
Claims
Application Information

- R&D Engineer
- R&D Manager
- IP Professional
- Industry Leading Data Capabilities
- Powerful AI technology
- Patent DNA Extraction
Browse by: Latest US Patents, China's latest patents, Technical Efficacy Thesaurus, Application Domain, Technology Topic, Popular Technical Reports.
© 2024 PatSnap. All rights reserved.Legal|Privacy policy|Modern Slavery Act Transparency Statement|Sitemap|About US| Contact US: help@patsnap.com