Diphenylamine alkylation catalyst and preparation method thereof
A diphenylamine alkane and catalyst technology, which is applied in the field of acid-containing solid diphenylamine alkylation catalyst and its preparation, can solve the problems of large catalyst usage, poor activity, and no mention of diphenylamine content, etc., and achieve reusable performance Good, with less dosage, the effect of increasing output
- Summary
- Abstract
- Description
- Claims
- Application Information
AI Technical Summary
Problems solved by technology
Method used
Image
Examples
preparation example Construction
[0017] The preparation method of the catalyst provided by the invention comprises the steps of saturated impregnating molecular sieves with aqueous acid solution, followed by dehydration and drying.
[0018] The aqueous solution concentration of the acid used in the method of the present invention is preferably 1-20% by mass, preferably 1-12% by mass, more preferably 1-10% by mass. The temperature of saturated impregnation is 20-80°C, and the impregnation time is preferably 2-7 hours. The drying temperature is 90-200°C. The saturated impregnation means that the volume of the impregnating liquid used is equal to the saturated adsorbed water amount of the impregnated carrier, and the impregnating liquid just wets the surface of the carrier completely.
[0019] The method for alkylating diphenylamine of the present invention comprises making diphenylamine contact and react with an alkylating agent at 140-250° C., 0.2-0.5 MPa, and an inert gas environment in the presence of the c...
example 1
[0030] (1) Preparation of catalyst
[0031] Take the HY type molecular sieve, press the liquid / solid ratio of 0.80ml / g at 20 DEG C, impregnate with the sulfuric acid solution saturation that concentration is 2 mass % for 2 hours, then distill off the water, dry 2 hours at 100 DEG C, obtain catalyst A, wherein sulfuric acid The content is 1.54% by mass, and the content of HY molecular sieve is 98.46% by mass.
[0032] (2) Preparation of alkylated diphenylamine
[0033]In a 250 ml autoclave, add 50.7 g of diphenylamine, 60.5 g of diisobutylene, and 2 g of catalyst A, and replace the reaction system with nitrogen three times. Stirring was started after the temperature was raised to 100°C, and the heating was continued to raise the temperature to 170°C. When the pressure of the reaction system reached 0.30 MPa, the reaction was timed for 10 hours. As the reaction progressed, the pressure was gradually reduced to 0.17 MPa, and when the content of diphenylamine in the reaction sys...
example 2
[0035] (1) Preparation of catalyst
[0036] Take the HY type molecular sieve, press the liquid / solid ratio of 0.78ml / g at 30 DEG C, impregnate with the sulfuric acid solution saturation that concentration is 4 mass % for 3 hours, then distill off water, 120 DEG C dry for 3 hours, obtain catalyst B, wherein sulfuric acid The content is 3.10% by mass, and the content of HY molecular sieve is 96.90% by mass.
[0037] (2) Preparation of alkylated diphenylamine
[0038] In a 250 ml autoclave, 50.7 g of diphenylamine, 67.2 g of diisobutylene, and 3 g of catalyst B were added, and the reaction system was replaced with nitrogen three times. After heating up to 100°C, start stirring, continue to heat up to 170°C, and when the pressure of the reaction system reaches 0.38MPa, time the reaction for 12 hours. As the reaction progresses, the pressure gradually decreases to 0.15MPa. When the diphenylamine content is less than 4% by mass, the reaction is terminated. Cool the material, and ...
PUM
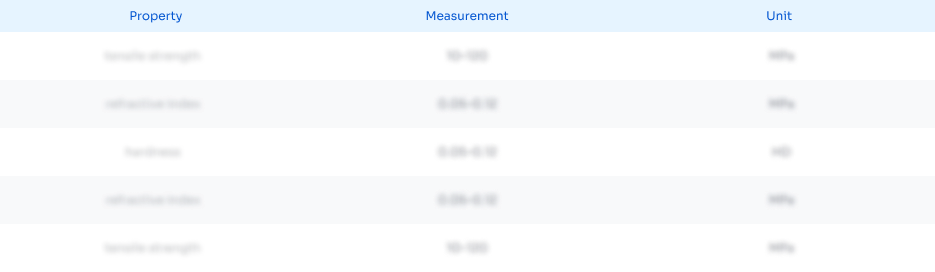
Abstract
Description
Claims
Application Information

- R&D Engineer
- R&D Manager
- IP Professional
- Industry Leading Data Capabilities
- Powerful AI technology
- Patent DNA Extraction
Browse by: Latest US Patents, China's latest patents, Technical Efficacy Thesaurus, Application Domain, Technology Topic, Popular Technical Reports.
© 2024 PatSnap. All rights reserved.Legal|Privacy policy|Modern Slavery Act Transparency Statement|Sitemap|About US| Contact US: help@patsnap.com