Crystal blank automatic grinding and polishing system, grinding and polishing machine and auxiliary machine thereof
A technology of blanks and crystals, which is applied in the field of grinding and polishing of crystal products. It can solve problems such as difficulty in consistency, high requirements for machine manufacturing precision, and difficulties in transportation and manufacturing. It can simplify the complexity of actions, ensure the quality of grinding and polishing, and facilitate The effect of manufacturing and maintenance
- Summary
- Abstract
- Description
- Claims
- Application Information
AI Technical Summary
Problems solved by technology
Method used
Image
Examples
Embodiment 1
[0025] Such as figure 1 A kind of crystal blank automatic grinding and polishing system shown, comprises: the first rotating frame 2, is provided with two upper hemisphere grinding stations 11 that grind the upper hemisphere of crystal blank around the first rotating frame 2 , 12 and an upper hemisphere polishing station 13, a waiting station 14 that the upper hemisphere of the crystal blank is polished, the first rotating frame 2 can rotate and locate and is provided with four heads 21; the second rotating frame 7. Two lower hemisphere grinding stations 61, 62 for grinding the lower hemisphere of the crystal blank and a lower hemisphere polisher for polishing the lower hemisphere of the crystal blank are provided around the second rotating frame 7 Position 63, a waiting station 64, the second rotating frame 7 can rotate and locate and is provided with four machine heads 71; The feeding station 41 is provided with a feeding mechanism that can fix the crystal blank on the clamp...
Embodiment 2
[0030] Such as Figure 4 A kind of crystal blank automatic grinding and polishing system shown, comprises: the first rotating frame 2, is provided with two upper hemisphere grinding stations 11 that grind the upper hemisphere of crystal blank around the first rotating frame 2 , 12 and an upper hemisphere polishing station 13, a waiting station 14 that the upper hemisphere of the crystal blank is polished, the first rotating frame 2 can rotate and locate and is provided with four heads 21; the second rotating frame 7. Two lower hemisphere grinding stations 61, 62 for grinding the lower hemisphere of the crystal blank and a lower hemisphere polisher for polishing the lower hemisphere of the crystal blank are provided around the second rotating frame 7 Position 63, a waiting station 64, the second rotating frame 7 can rotate and locate and is provided with four machine heads 71; The feeding station 41 is provided with a feeding mechanism that can fix the crystal blank on the clam...
PUM
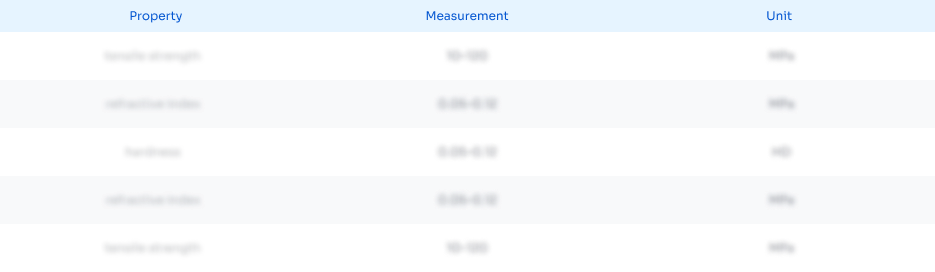
Abstract
Description
Claims
Application Information

- R&D
- Intellectual Property
- Life Sciences
- Materials
- Tech Scout
- Unparalleled Data Quality
- Higher Quality Content
- 60% Fewer Hallucinations
Browse by: Latest US Patents, China's latest patents, Technical Efficacy Thesaurus, Application Domain, Technology Topic, Popular Technical Reports.
© 2025 PatSnap. All rights reserved.Legal|Privacy policy|Modern Slavery Act Transparency Statement|Sitemap|About US| Contact US: help@patsnap.com