Forming and pressing die for loudspeaker drum paper
A technology for pressing molds and forming molds, applied in the directions of forming tools, manufacturing tools, sensors, etc., can solve the problems of operator and enterprise injury, prone to industrial accidents, prone to wrinkles, etc., to reduce waste and defective products, eliminate The effect of suppressing wrinkles and improving safety
- Summary
- Abstract
- Description
- Claims
- Application Information
AI Technical Summary
Problems solved by technology
Method used
Image
Examples
Embodiment Construction
[0012] Specific embodiments of the present invention will be described below in conjunction with the accompanying drawings.
[0013] Such as image 3 , Figure 4 As shown, said loudspeaker drum paper forming pressing mold includes an upper mold part and a lower mold part. The head 3 is fixedly installed on the lower end surface of the upper template 2. The upper die head 3 is composed of an upper forming surface 31 and an upper pressure ring 32. The shape of the upper forming surface 31 is consistent with the shape of the upper end surface of the drum paper, and the width of the upper pressure ring 32 is Greater than the width of the blank holder 93 of the drum paper, the distance between the upper press ring 32 and the upper forming surface 31 is equal to the height of the cone 91 of the drum paper; Template 7, lower die head 4 is made up of molding die body 41 and bearing column 42, and molding die body 41 is made up of lower molding surface 43 and lower pressure ring 44, ...
PUM
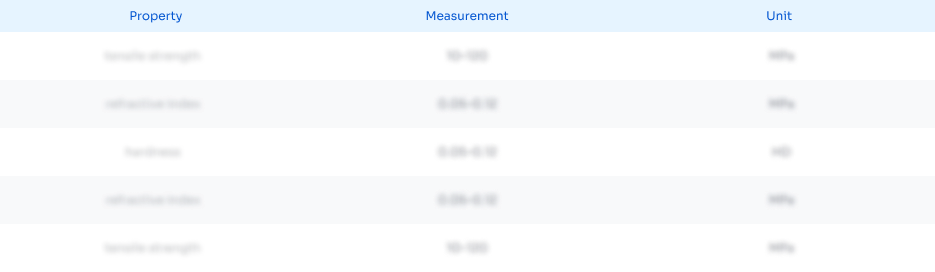
Abstract
Description
Claims
Application Information

- Generate Ideas
- Intellectual Property
- Life Sciences
- Materials
- Tech Scout
- Unparalleled Data Quality
- Higher Quality Content
- 60% Fewer Hallucinations
Browse by: Latest US Patents, China's latest patents, Technical Efficacy Thesaurus, Application Domain, Technology Topic, Popular Technical Reports.
© 2025 PatSnap. All rights reserved.Legal|Privacy policy|Modern Slavery Act Transparency Statement|Sitemap|About US| Contact US: help@patsnap.com