Force feedback type underwater cable guider
An underwater cable and force feedback technology, applied in cable laying equipment, electrical components, etc., can solve the problems of low tension control accuracy, influence of cable laying quality, slow response speed, etc., to avoid cable dragging and reliable performance. , the effect of easy maintenance
- Summary
- Abstract
- Description
- Claims
- Application Information
AI Technical Summary
Problems solved by technology
Method used
Image
Examples
Embodiment 1
[0018] Embodiment 1: as figure 1 , figure 2 As shown, the present invention includes a guide frame 1 and four force feedback mechanisms 2 connected with the guide frame 1. The guide frame 1 is provided with through holes 15 for passing cables 13 in the axial direction, and is symmetrical in pairs in the radial direction. There are four radial slots 18 communicating with the axial through holes in a cross shape. The four force feedback mechanisms 2 are installed in the radial slots 18 and extend into the axial through holes 15. When in use, the cables 13 pass through Through the axial through hole 15 of the guide frame 1, the signal output terminals of the four force feedback mechanisms 2 communicate with the external control system respectively.
[0019] like figure 2 As shown, the force feedback mechanism 2 includes a roller 4, a tension pressure sensor 7, a guiding and fixed base plate 12, a sealed cabin body 9, a roller bracket 16 and a connecting stud 6, and the tensio...
Embodiment 2
[0026] Embodiment 2: The structure of this embodiment is the same as that of Embodiment 1, except that the angle α between the roller 4 of the force feedback mechanism 2 and the cable 13 and the tangent line of the arc surface of the guide frame 1 is 20°.
Embodiment 3
[0027] Embodiment 3: The structure of this embodiment is the same as that of Embodiment 1, except that the angle α between the roller 4 and the cable 13 of the force feedback mechanism 2 and the arc tangent of the guide frame 1 is 22°.
PUM
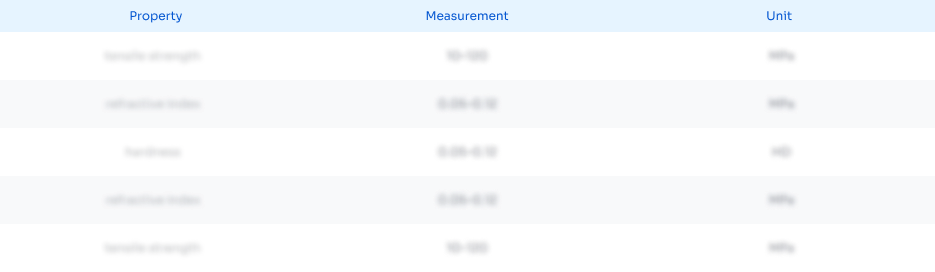
Abstract
Description
Claims
Application Information

- R&D Engineer
- R&D Manager
- IP Professional
- Industry Leading Data Capabilities
- Powerful AI technology
- Patent DNA Extraction
Browse by: Latest US Patents, China's latest patents, Technical Efficacy Thesaurus, Application Domain, Technology Topic, Popular Technical Reports.
© 2024 PatSnap. All rights reserved.Legal|Privacy policy|Modern Slavery Act Transparency Statement|Sitemap|About US| Contact US: help@patsnap.com