Thrusting rod bench simulation fatigue tester
A fatigue test, thrust rod technology, applied in the testing of mechanical components, testing of machine/structural components, measuring devices, etc., can solve the problems of long test cycle and low test accuracy
- Summary
- Abstract
- Description
- Claims
- Application Information
AI Technical Summary
Problems solved by technology
Method used
Image
Examples
Embodiment Construction
[0012] Such as figure 1 , figure 2 , image 3 As shown, the thrust rod bench simulation fatigue testing machine includes a workbench 1, a front support seat 6 arranged at the front end of the workbench 1, a rear support seat 15 arranged at the rear end of the workbench 1, and a rear support seat 15 mounted on the rear end of the workbench 1. Shaft 16, the front shaft 11 that passes through the front support seat 6, the clutch 13 that is located between the rear shaft 16 and the front shaft 11, the front holder 52 that is located on the inside of the front shaft 11, and the front holder 52 that is located at the inner end of the front holder. Front rotating cam 5, two front U-shaped connection seats 51 located on the left and right sides of the preceding rotating cam 5, the rear fixed seat 161 located on the inside of the rear axle 16, the rear rotating cam 3 located at the rear fixed seat 161 inner end, located at Two rear U-shaped connecting seats 31 on the left and right ...
PUM
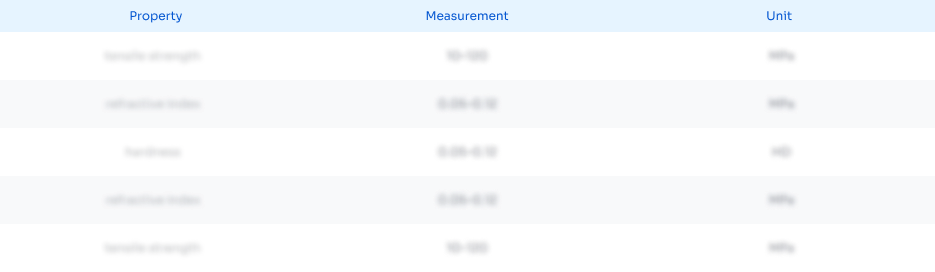
Abstract
Description
Claims
Application Information

- R&D Engineer
- R&D Manager
- IP Professional
- Industry Leading Data Capabilities
- Powerful AI technology
- Patent DNA Extraction
Browse by: Latest US Patents, China's latest patents, Technical Efficacy Thesaurus, Application Domain, Technology Topic, Popular Technical Reports.
© 2024 PatSnap. All rights reserved.Legal|Privacy policy|Modern Slavery Act Transparency Statement|Sitemap|About US| Contact US: help@patsnap.com