Composite material elbow winding machine control mechanism and winding method thereof
A composite material and control mechanism technology, applied in other home appliances, home appliances, applications, etc., can solve the problems of high cost, complex mechanical structure and trajectory planning, achieve stable product performance, break through the bottleneck of the overall structure, and reduce costs. Effect
- Summary
- Abstract
- Description
- Claims
- Application Information
AI Technical Summary
Problems solved by technology
Method used
Image
Examples
Embodiment 1
[0020] Composite material elbow winding machine control mechanism, its composition includes: main shaft three-phase asynchronous motor 1, said main shaft three-phase asynchronous motor is connected to main shaft 3 through main shaft reducer 2, and said main shaft is correspondingly connected to elbow mandrel 4, so The mandrel of the bent pipe is corresponding to the composite material 5 impregnated with resin, and the composite material is wound on the wire guide head 6, and the wire guide head is driven by a winding trolley 8 with an operating handle 7, and the winding trolley Connect dipping tank 9.
Embodiment 2
[0022] In the control mechanism of the composite material elbow winding machine, the three-phase asynchronous motor of the main shaft is connected to the main shaft reducer, and the main shaft reducer and the main shaft are respectively connected by a set of gears 10 meshing with each other.
Embodiment 3
[0024] The winding method of the control mechanism of the composite material elbow winding machine controls the speed and direction of the main shaft through the potentiometer, and pushes the position control handle on the trolley to control the reciprocating swing of the trolley, so that the main shaft drives the rotation and rotation of the mandrel of the elbow. The winding trolley drives the wire guide head of the composite material to reciprocate and swing along the axis of the elbow mandrel in a semi-circular orbit, and the composite of the two, the composite material impregnated with resin is regularly wound on the surface of the elbow mandrel, and formed after multi-layer winding Composite material winding layer, after the winding is completed, take off the elbow mandrel to form a composite material elbow.
PUM
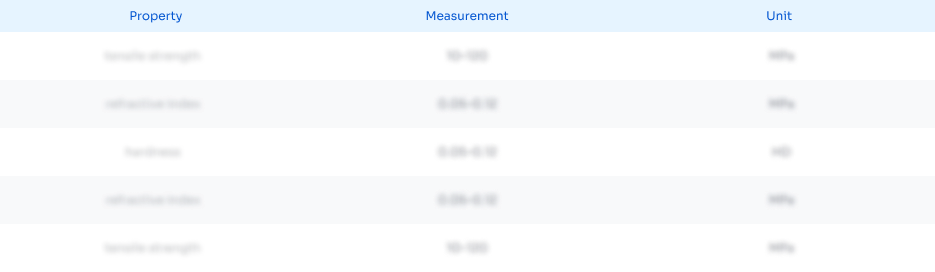
Abstract
Description
Claims
Application Information

- R&D
- Intellectual Property
- Life Sciences
- Materials
- Tech Scout
- Unparalleled Data Quality
- Higher Quality Content
- 60% Fewer Hallucinations
Browse by: Latest US Patents, China's latest patents, Technical Efficacy Thesaurus, Application Domain, Technology Topic, Popular Technical Reports.
© 2025 PatSnap. All rights reserved.Legal|Privacy policy|Modern Slavery Act Transparency Statement|Sitemap|About US| Contact US: help@patsnap.com