Resonance type optical fiber F-P sensor and method of producing same
A manufacturing method and resonant technology, which are applied in the direction of using optical devices to transmit sensing components, etc., can solve the problems of limited measurement accuracy, low production efficiency, poor reflection performance, etc., and achieve the effect of good optical performance.
- Summary
- Abstract
- Description
- Claims
- Application Information
AI Technical Summary
Problems solved by technology
Method used
Image
Examples
Embodiment 1
[0022] Step 1, use a 157nm ultraviolet laser to process a cylindrical groove 2 with a diameter of 40 microns on the end face of a single-mode silica fiber, with a depth of 30 microns, such as figure 1 As shown, a layer of photothermal film 3 is plated on the bottom of the tank 2 as an excitation medium;
[0023] Step 2. Splice a section of single-mode quartz optical fiber 1 outside the groove 2 processed in step 1 by an arc of an ordinary fusion splicer, and the groove 2 forms a F-P cavity 5. As shown in FIG. 2 , the reflection spectrum of the F-P cavity 5 of the optical fiber Such as Figure 9 As shown, the reflection fringe contrast is over 20dB;
[0024] Step 3, cutting the optical fiber at the outer end face of the Fab cavity 5 to form a Fab resonator film 6, then welding the protective optical fiber 7 with a microgroove 9 on the end face at the outer end of the resonator film 6 to protect the Fab resonator film 6, and then The resonant optical fiber FAP sensor of the pr...
Embodiment 2
[0028] Step 1. Machining a cylindrical groove 2 with a diameter of 70 microns and a depth of 60 microns on the end face of the multimode optical fiber 1 with a femtosecond laser;
[0029] Step 2, processing an optical fiber with a diameter of 40 microns with a protrusion 8 on the end face of the multimode optical fiber with a femtosecond laser, as shown in Figure 4;
[0030] Step 3. The optical fiber 1 processed in step 1 is arc-fused to the optical fiber processed in step 2 through a fusion splicer, and the end with the protrusion 8 is docked with the end with the cylindrical groove 2 to form an optical fiber Fab cavity 5 with a hard center of mass, such as As shown in FIG. 5 , the hard mass center is the above-mentioned protrusion 8 . The reflectance spectrogram of this optical fiber Fab cavity 5 is as follows Figure 10 As shown, the reflection fringe contrast is over 23dB;
[0031] Step 4. On the basis of step 3, cut the optical fiber at the outer end face of the Fab cav...
PUM
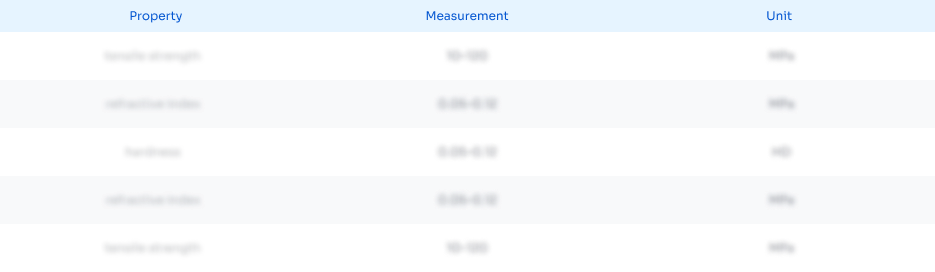
Abstract
Description
Claims
Application Information

- R&D Engineer
- R&D Manager
- IP Professional
- Industry Leading Data Capabilities
- Powerful AI technology
- Patent DNA Extraction
Browse by: Latest US Patents, China's latest patents, Technical Efficacy Thesaurus, Application Domain, Technology Topic, Popular Technical Reports.
© 2024 PatSnap. All rights reserved.Legal|Privacy policy|Modern Slavery Act Transparency Statement|Sitemap|About US| Contact US: help@patsnap.com