Method for synthesis of 4A molecular sieve with coal ash alkali melting method
A technology of fly ash and molecular sieve, which is applied in related technical fields, can solve the problems of long reaction route, high production cost and high equipment requirements, and achieve the effects of improving utilization rate, good gelling performance and reducing alkali consumption
- Summary
- Abstract
- Description
- Claims
- Application Information
AI Technical Summary
Problems solved by technology
Method used
Examples
Embodiment 1
[0024] Take Al 2 o 3 36% to 46%, SiO 2 / Al 2 o 3 Fly ash with a molar ratio between 1.8 and 2.1 is used as raw material, take 34g NaOH, and 20g fly ash according to NaOH 2 O / Al 2 o 3 Mix with alkali at a molar ratio of 3 to 10, remove impurities from the mixed material, and charge the finely mixed mixture in a high-temperature furnace at 600°C for 2 hours for activation. The height of the mixture in the high-temperature furnace is controlled at Each layer is 5cm, take it out and extract it with water after cooling, and control the H 2 O / Na 2 The molar ratio of O is 60, stirred at 80°C for 1.5 hours to form a gel, then raised to 95°C and left to stand at a constant temperature for 5 hours to crystallize, filtered with suction, washed to pH = 11, and dried to obtain 4A molecular sieve product. Tests have proved that the 4A molecular sieve of this embodiment has a calcium exchange capacity of 316.3mg CaCO 3 / g and the sieving rate through a 1.25mm sieve is not less than ...
Embodiment 2
[0026] In order to further examine the various parameters involved in the process, the difference between this embodiment and Example 1 is that the temperature of the high-temperature furnace is adjusted to 800°C, the calcination activation time is 1 hour, and the height of the mixture charge in the high-temperature furnace is controlled at Layer 8cm, then raise the temperature to 110°C and let stand at a constant temperature for 4 hours to crystallize, filter with suction, wash the crystals until pH = 10, and the rest are the same as in Example 1. Tests have proved that the calcium exchange capacity of the obtained 4A molecular sieve is the same as that in Example 1. .
Embodiment 3
[0028] The difference between this example and Example 1 is that the temperature of the high-temperature furnace is adjusted to 550° C., the calcination activation time is 3 hours, the height of the mixture charge in the high-temperature furnace is controlled at 4 cm per layer, and the crystallization time at constant temperature is After 6 hours, add water to dissolve the mixed material and stir for 2 hours at 55°C to form a gel, then raise the temperature to 100°C, stand at constant temperature for 6 hours to crystallize, filter with suction, wash the crystals until pH = 9, and the rest are the same as in Example 1. The obtained 4A molecular sieve has been tested and proved to have the same calcium exchange capacity as that in Example 1.
[0029] It should be noted that the present invention is not limited to the above examples, for example, after dissolving in water, controlling H 2 O / Na 2 The molar ratios of O are 30, 40 and 50 respectively, and the obtained 4A molecular ...
PUM
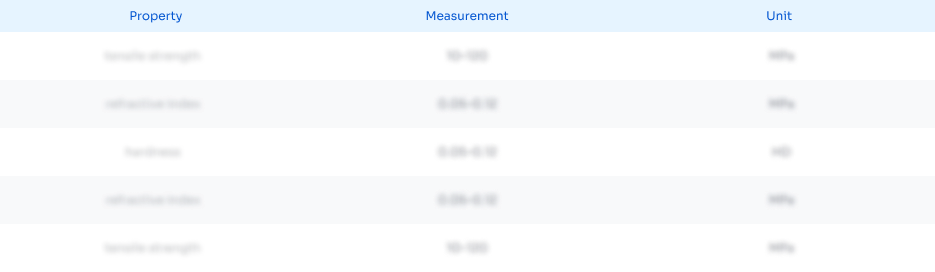
Abstract
Description
Claims
Application Information

- Generate Ideas
- Intellectual Property
- Life Sciences
- Materials
- Tech Scout
- Unparalleled Data Quality
- Higher Quality Content
- 60% Fewer Hallucinations
Browse by: Latest US Patents, China's latest patents, Technical Efficacy Thesaurus, Application Domain, Technology Topic, Popular Technical Reports.
© 2025 PatSnap. All rights reserved.Legal|Privacy policy|Modern Slavery Act Transparency Statement|Sitemap|About US| Contact US: help@patsnap.com