Method for smoothing speed of high speed numerical control processing track corner
A technology for processing trajectory and corners, applied in the direction of digital control, electrical program control, etc., can solve the problems of large contour error, speed response, unsatisfactory processing efficiency, and cannot well meet the requirements of high-speed processing, etc., to achieve speed, The effect of ensuring machining accuracy
- Summary
- Abstract
- Description
- Claims
- Application Information
AI Technical Summary
Problems solved by technology
Method used
Image
Examples
Embodiment 1
[0021] The two straight-line processing sections S1 and S2 are shown in Fig. 4, since the two processing sections are not on a straight line, an inflection point is formed, and σ is the supplementary angle of the corner of the two processing sections. Assume is the unit vector at the end of the first processing segment S1, is the unit vector at the beginning of the second processing segment S2, then: σ = v 1 → · v 2 → , Therefore: corner 2θ=π-σ. After a deceleration motion with a distance of d, the speed of the processing section S1 drops to zero; assuming that the shortest distance (contour error) from the corner vertex to the transition curve is δ, we can get: d = 2 δ cos θ ...
Embodiment 2
[0024] Straight line processing section S1 and arc processing section S2 such as figure 2 As shown, since the two processing sections are not on a straight line, an inflection point is formed, and σ is the supplementary angle of the corner of the two processing sections. Assume is the unit vector at the end of the first processing segment S1, is the unit vector of the tangent line at the starting point of the second processing segment S2, then: σ = v 1 → · v 2 → , Therefore: corner 2θ=π-σ. After a deceleration motion with a distance of d, the speed of the processing section S1 drops to zero; assuming that the shortest distance (contour error) from the corner vertex to the transition curve is δ, it can be obtained as follows: d = 2 δ ...
Embodiment 3
[0027] Arc processing segment S1 and arc processing segment S2 are as image 3 As shown, since the two processing sections are not on a straight line, an inflection point is formed, and σ is the supplementary angle of the corner of the two processing sections. Assume is the unit vector of the tangent line at the end point of the first processing segment S1, is the unit vector of the tangent line at the starting point of the second processing segment S2, then: σ = v 1 → · v 2 → , Therefore: corner 2θ=π-σ. After a deceleration motion with a distance of d, the speed of the processing section S1 drops to zero; assuming that the shortest distance (contour error) from the corner vertex to the transition curve is δ, it can be obtained as follows: d = 2 ...
PUM
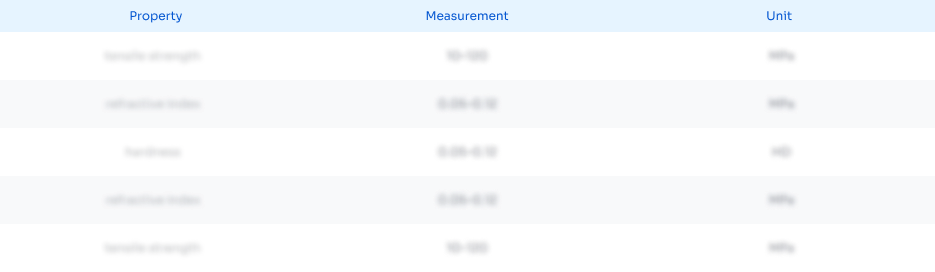
Abstract
Description
Claims
Application Information

- Generate Ideas
- Intellectual Property
- Life Sciences
- Materials
- Tech Scout
- Unparalleled Data Quality
- Higher Quality Content
- 60% Fewer Hallucinations
Browse by: Latest US Patents, China's latest patents, Technical Efficacy Thesaurus, Application Domain, Technology Topic, Popular Technical Reports.
© 2025 PatSnap. All rights reserved.Legal|Privacy policy|Modern Slavery Act Transparency Statement|Sitemap|About US| Contact US: help@patsnap.com