Simulation system implementing real-time machine data
a simulation system and machine data technology, applied in the field of simulation systems, can solve the problems of limited and costly use of onboard operators, ineffective, time-consuming and labor-intensive, etc., and achieve the effects of reducing the risk of accidents, reducing the efficiency of the system, and increasing the cost of operation
- Summary
- Abstract
- Description
- Claims
- Application Information
AI Technical Summary
Problems solved by technology
Method used
Image
Examples
Embodiment Construction
[0014]FIG. 1 illustrates an exemplary machine 10 performing a predetermined function at a worksite 12. Machine 10 may embody a stationary or mobile machine, with the predetermined function being associated with a particular industry such as mining, construction, farming, transportation, power generation, or any other industry known in the art. For example, machine 10 may be an earth moving machine such as the excavator depicted in FIG. 1, in which the predetermined function includes the removal of earthen material from worksite 12 that alters the geography of worksite 12 to an architecturally desired form. Machine 10 may alternatively embody a different earth moving machine such as a motor grader or a wheel loader, or a non-earth moving machine such as a passenger vehicle, a stationary generator set, or a pumping mechanism. Machine 10 may embody any suitable operation-performing machine.
[0015]As illustrated in FIG. 2, machine 10 may include a simulation system 14 having multiple com...
PUM
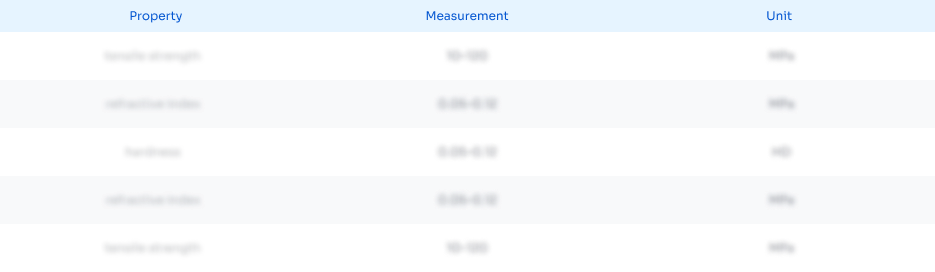
Abstract
Description
Claims
Application Information

- R&D
- Intellectual Property
- Life Sciences
- Materials
- Tech Scout
- Unparalleled Data Quality
- Higher Quality Content
- 60% Fewer Hallucinations
Browse by: Latest US Patents, China's latest patents, Technical Efficacy Thesaurus, Application Domain, Technology Topic, Popular Technical Reports.
© 2025 PatSnap. All rights reserved.Legal|Privacy policy|Modern Slavery Act Transparency Statement|Sitemap|About US| Contact US: help@patsnap.com