Oil well polish rod clamp for use with a rotator on a beam pumping unit
a technology for polishing rods and beam pumps, which is applied in the direction of drilling casings, wells, drilling pipes, etc., can solve the problems of reducing the service life of the beam pumping unit, affecting the service life of the pumping unit, so as to increase the longitudinal or axial gripping capacity, reduce the contact area, and increase the gripping pressure
- Summary
- Abstract
- Description
- Claims
- Application Information
AI Technical Summary
Benefits of technology
Problems solved by technology
Method used
Image
Examples
Embodiment Construction
[0017]Referring now to FIG. 1, oil well polish rod clamp 10 of the present invention includes a unitary and generally cylindrical housing 12 with a central bore sized to receive a polish rod 14. FIG. 1 illustrates the lower portion of the horsehead 16 of a beam pumping unit, an accessory carrier bar 18, which is a transverse cross member with a hole sized to allow the polish rod 14 to pass therethrough, and a rod rotator 20 mounted above the carrier bar 18. For the depicted embodiment, the rod rotator has a simple handle 22 for manually rotating the rod. Bridle 24 extends in the conventional manner between the horsehead and the carrier bar, and for small pumping units provides a minimum space between the bridle cables.
[0018]By providing a unitary, monolithic, donut-shaped body, the clamping mechanism associated with a split body and a hinge on one side and bolts or other clamping members on the opposing side are avoided. Also, reliable gripping engagement between the rod and the hou...
PUM
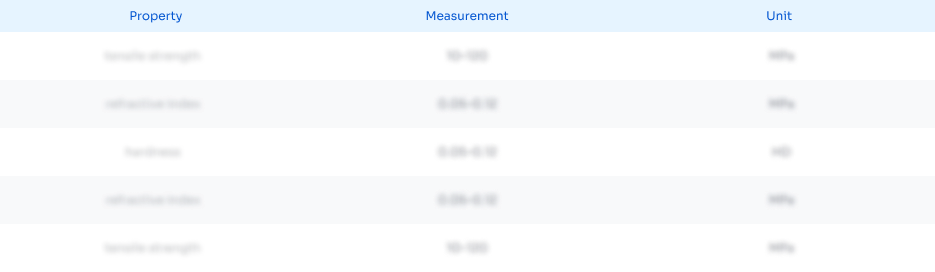
Abstract
Description
Claims
Application Information

- R&D
- Intellectual Property
- Life Sciences
- Materials
- Tech Scout
- Unparalleled Data Quality
- Higher Quality Content
- 60% Fewer Hallucinations
Browse by: Latest US Patents, China's latest patents, Technical Efficacy Thesaurus, Application Domain, Technology Topic, Popular Technical Reports.
© 2025 PatSnap. All rights reserved.Legal|Privacy policy|Modern Slavery Act Transparency Statement|Sitemap|About US| Contact US: help@patsnap.com