Turbo Machine
a technology of rotating wheels and rotating shafts, which is applied in the direction of liquid fuel engines, vessel construction, marine propulsion, etc., can solve the problems of high repair costs, increased wear, and certain tendency to oscillate, so as to improve aerodynamics and facilitate the removal of the shroud for maintenance or repair purposes
- Summary
- Abstract
- Description
- Claims
- Application Information
AI Technical Summary
Benefits of technology
Problems solved by technology
Method used
Image
Examples
Embodiment Construction
[0036]According to FIG. 1, a turbo machine 1 is equipped with a rotor 2 and with a stator 3. The rotor 2 is mounted rotatably in the stator 3 in the usual way. The turbo machine 1 may basically be a compressor or a turbine. Where a turbine is concerned, it may be a steam turbine or a gas turbine. The turbo machine 1 may be stationary and serve, for example, for driving a generator in a power plant. The turbo machine 1 may likewise be a drive assembly in a vehicle, in particular in an aircraft. However, an implementation of the invention in a configuration of the turbo machine 1 as a stationary gas turbine is preferred.
[0037]The rotor 2 has, according to FIG. 1, at least one moving blade row 4 which include a plurality of moving blades 5. The cross section according to FIG. 1 lies in the region of such a moving blade row 4, although only a single moving blade 5 is illustrated for the sake of clarity.
[0038]Moreover, the turbo machine 1 is equipped at least with a shroud 8. This shroud...
PUM
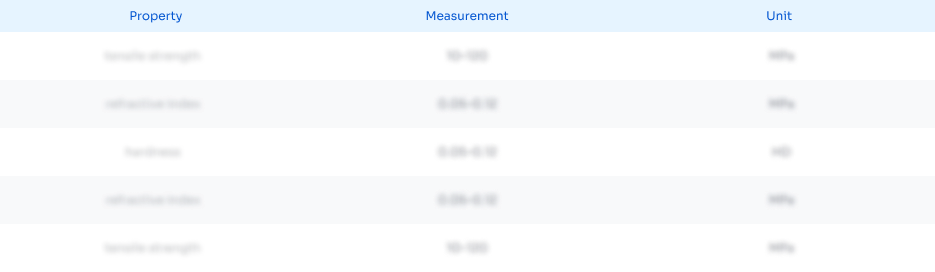
Abstract
Description
Claims
Application Information

- R&D
- Intellectual Property
- Life Sciences
- Materials
- Tech Scout
- Unparalleled Data Quality
- Higher Quality Content
- 60% Fewer Hallucinations
Browse by: Latest US Patents, China's latest patents, Technical Efficacy Thesaurus, Application Domain, Technology Topic, Popular Technical Reports.
© 2025 PatSnap. All rights reserved.Legal|Privacy policy|Modern Slavery Act Transparency Statement|Sitemap|About US| Contact US: help@patsnap.com