Composite seat back frame
a composite seat and frame technology, applied in the field of modular composite seat back frames, can solve the problems of increasing cost reducing the overall weight of the airplane,
- Summary
- Abstract
- Description
- Claims
- Application Information
AI Technical Summary
Benefits of technology
Problems solved by technology
Method used
Image
Examples
Embodiment Construction
[0016]While the present invention is described with reference to embodiments described herein, it should be clear that the present invention is not limited to such embodiments. Therefore, the description of the embodiments herein is merely illustrative of the present invention and will not limit the scope of the invention as claimed.
[0017]As generally described herein, FIGS. 1-7 illustrate embodiments of a composite seat back assembly 10 (hereinafter referred to as “the seat back 10”). In one embodiment, as shown in FIG. 1, the seat back 10 generally comprises a body 20 and one or more legs 30 secured thereto. The configuration of the body 20 and the leg 30 and the composite structure of one or both provides improved structural stability while decreasing the number of parts and overall weight of the seat back 10. Accordingly, the seat back 10 is capable of being utilized in airplanes. In a preferred embodiment, the body 20 and the leg 30 may be formed from composite blanks, as descr...
PUM
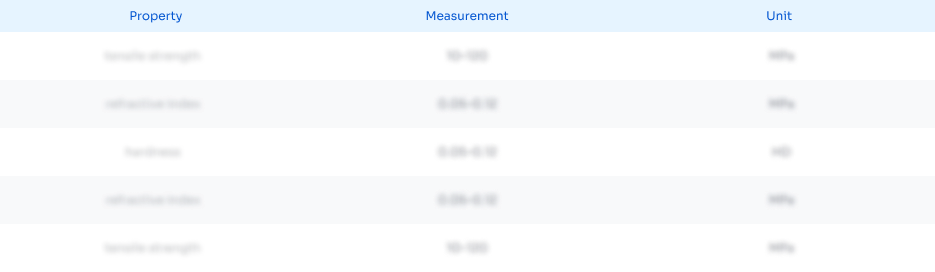
Abstract
Description
Claims
Application Information

- R&D
- Intellectual Property
- Life Sciences
- Materials
- Tech Scout
- Unparalleled Data Quality
- Higher Quality Content
- 60% Fewer Hallucinations
Browse by: Latest US Patents, China's latest patents, Technical Efficacy Thesaurus, Application Domain, Technology Topic, Popular Technical Reports.
© 2025 PatSnap. All rights reserved.Legal|Privacy policy|Modern Slavery Act Transparency Statement|Sitemap|About US| Contact US: help@patsnap.com