Method for operating a surgical stapling and cutting device
a cutting device and surgical stapling technology, applied in the field of surgical stapling instruments, can solve the problems of inconvenient operation of the firing bar, limited control of the u.s. surgical corp. stapler, and distracting the clinician from the effect of the operation
- Summary
- Abstract
- Description
- Claims
- Application Information
AI Technical Summary
Benefits of technology
Problems solved by technology
Method used
Image
Examples
first embodiment
[0139]FIGS. 25 and 26 illustrate a second exemplary embodiment of the stapling and cutting system 200 according to the invention. This system 200 is different than the first embodiment in that the motorized stapling assembly is entirely contained in the end effector 210. Therefore, the handle 220 only needs to have two actuating devices. The first actuating device 222 is a ball joint releasing lever and the second actuating device is the stapling / cutting motor on / off button 224.
[0140] The end effector 210 is connected to the distal end of the actuation shaft 226 of the handle 220 at a ball-joint connector 228. The end effector 210 has, at its distal-most end, a ball joint 212. The ball joint 212 has two opposing cup-shaped clamps 2122, 2124. The interior surfaces of the clamps 2122, 2124 are shaped to correspond to the outer shape of the ball joint 212. The clamps 2122, 2124 translate towards or away from one another based upon an actuation of the lever 222.
[0141] The clamps 2122, ...
second embodiment
[0144]FIGS. 27 and 28 illustrate a variation of the end effector shown in FIGS. 25 and 26. In particular, the handle 220 is the same as in FIGS. 25 and 26. However, the end effector 310 is different. Specifically, the end effector 310 has a proximal ball joint 312 similar to the ball joint 212 in FIGS. 25 and 26, but also has a second, distal ball joint 314, having a shape virtually identical to the proximal ball joint 312. Therefore, when the lever 222 is pressed down to release the ball joint 312, 314, the end effector 310 can be allowed to rest within the body and the opposite end can be grasped between the clamps 2122, 2124. In such an orientation, shown in FIG. 27, the stapling / cutting can be actuated when the jaw opening is facing the user.
[0145] It is also noted that placement of an end effector 210, 310 at a surgical site sometimes requires the access to the surgical site to be rather small in comparison to the opened jaws of the end effector 210, 310. With the ability to re...
fourth embodiment
[0188]FIG. 54 shows some internal parts of this fourth embodiment of the end effector. The anvil 1020 is disposed opposite the staple cartridge holder 1030 and a closure ring 1040 surrounds the proximal end of the staple cartridge holder 1030. The inner and outer tubes 1130, 1110 are removed so that the articulation lock release slide 1120, the pushrod 1102, and the pushrod-blade support 1070 can be seen clearly. A screen door 1103 is mounted around the pushrod 1102 and inside the inner and outer tubes 1130, 1110 and the bell actuator 1100. The handle 1200 and bell actuator 1100 are removed for clarity. The screen door 1103 restricts movement of the pushrod 1102 to only one direction—distal—because the knife / cutting blade 1060 only moves in the distal direction.
[0189] The two-part clevis is best illustrated in the views of FIGS. 55 and 56. These figures show various internal features of the end effector of FIG. 54 with the outer tube 1110 removed. In the exploded view of FIG. 55, co...
PUM
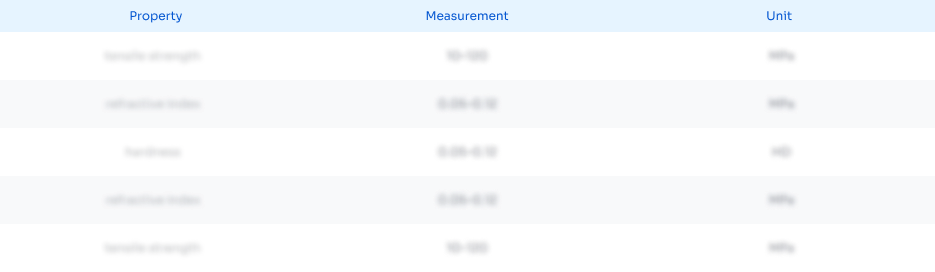
Abstract
Description
Claims
Application Information

- R&D
- Intellectual Property
- Life Sciences
- Materials
- Tech Scout
- Unparalleled Data Quality
- Higher Quality Content
- 60% Fewer Hallucinations
Browse by: Latest US Patents, China's latest patents, Technical Efficacy Thesaurus, Application Domain, Technology Topic, Popular Technical Reports.
© 2025 PatSnap. All rights reserved.Legal|Privacy policy|Modern Slavery Act Transparency Statement|Sitemap|About US| Contact US: help@patsnap.com