Bare die tray with flat datum surface
- Summary
- Abstract
- Description
- Claims
- Application Information
AI Technical Summary
Benefits of technology
Problems solved by technology
Method used
Image
Examples
Embodiment Construction
[0022] While the present invention will be described herein with reference to particular embodiments thereof, a latitude of modifications, various changes and substitutions are intended, and it will be appreciated that in some instances some features of the invention will be employed without a corresponding use of other features without departing from the spirit and scope of the invention as described with respect to the preferred embodiments set forth herein.
[0023] Referring now to FIGS. 2A and 2B, a component tray 22 is shown that has been formed in a mold. The tray 22 has a component housing portion 24 containing a plurality of component pockets 26 opening to top surface 28. A flange 30 extends around the housing portion 24, defining the perimeter of the tray 22. The flange 30 has a flange top surface 32, and a bottom surface 34 shown in FIG. 2B. The flange alternatively can be of other configurations, for example the flange could extend less than completely around the housing, ...
PUM
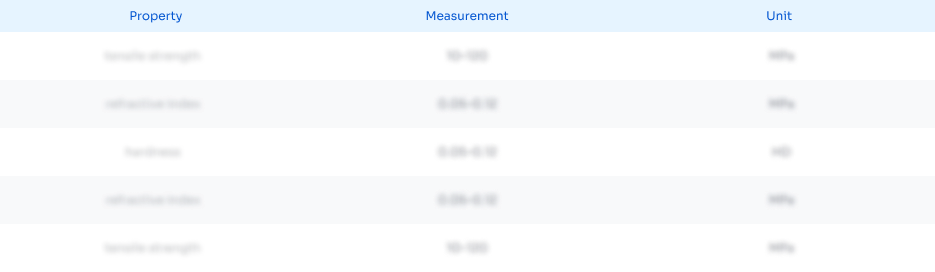
Abstract
Description
Claims
Application Information

- R&D
- Intellectual Property
- Life Sciences
- Materials
- Tech Scout
- Unparalleled Data Quality
- Higher Quality Content
- 60% Fewer Hallucinations
Browse by: Latest US Patents, China's latest patents, Technical Efficacy Thesaurus, Application Domain, Technology Topic, Popular Technical Reports.
© 2025 PatSnap. All rights reserved.Legal|Privacy policy|Modern Slavery Act Transparency Statement|Sitemap|About US| Contact US: help@patsnap.com