Method for producing self-adhesive elastic bandage
A self-adhesive elastic bandage, a technology for making method, applied in bandages, chemical instruments and methods, adhesives, etc., can solve the problems of low production efficiency, insufficiently uniform adhesive layer, low solid content of adhesives, etc. Uniform, moderately viscous effect
- Summary
- Abstract
- Description
- Claims
- Application Information
AI Technical Summary
Problems solved by technology
Method used
Examples
Embodiment 1
[0024] Get 100 kilograms of natural rubber latex that contains 65% natural rubber, 1.5 kilograms of polyacrylate latexes, be mixed with adhesive. Select a roll of elastic non-woven fabric with an elastic ratio of 1: 2.5, and fix it on the rear feeding frame. Unwind the non-woven fabric through the automatic edge-aligning device, pass it between the two sets of round rollers from bottom to top, and cause the transmission needle plate to be fixed. Adjust the gap between the two upper rubber rollers, adjust the system pressure of the two upper rubber rollers, and squeeze the non-woven fabric between the two upper rubber rollers. Pump the adhesive into the glue-holding areas on the two groups of round rollers respectively, start the double-sided glue coating machine, and control the coating speed to 10-15 m / min. With the transmission of the equipment, a certain thickness of glue is formed on the surface of the rubber rollers. Adhesive film, the adhesive is evenly coated on both s...
Embodiment 2
[0026] Get 100 kilograms of natural rubber emulsion that contains 60% natural rubber, 2 kilograms of polyurethane emulsions, be mixed with adhesive. Select a roll of elastic cotton cloth with an elastic ratio of 1: 2.3, and fix it on the rear feeding frame. Unwind the elastic cotton cloth through the automatic side-aligning device, pass it between the two sets of round rollers from bottom to top, and cause the transmission needle plate to be fixed. Adjust the gap between the two upper rubber rollers, adjust the system pressure of the two upper rubber rollers, and squeeze the elastic cotton cloth between the two upper rubber rollers. Pump the adhesive into the glue-holding areas on the two groups of round rollers respectively, start the double-sided glue coating machine, and control the coating speed to 20-25 m / min. With the transmission of the equipment, a certain thickness of glue is formed on the surface of the rubber rollers. Adhesive film, through the extrusion of two upp...
Embodiment 3
[0028] Get 100 kilograms of natural rubber latex that contains 50% natural rubber, 3 kilograms of polyacrylate latexes, be mixed with adhesive. A roll of elastic gauze with an elastic ratio of 1: 2.8 is selected and fixed on the rear feeding frame. Unwind the elastic gauze through the automatic side-aligning device, and pass it between the two sets of round rollers from bottom to top, and cause the transmission needle plate to be fixed. Adjust the gap between the two upper rubber rollers, adjust the system pressure of the two upper rubber rollers, and squeeze the elastic gauze between the two upper rubber rollers. Pump the adhesive into the glue-holding areas on the two groups of round rollers respectively, start the double-sided glue coating machine, and control the coating speed to 30-35 m / min. With the transmission of the equipment, a certain thickness of glue is formed on the surface of the rubber rollers. Adhesive film, the adhesive is evenly coated on both surfaces of t...
PUM
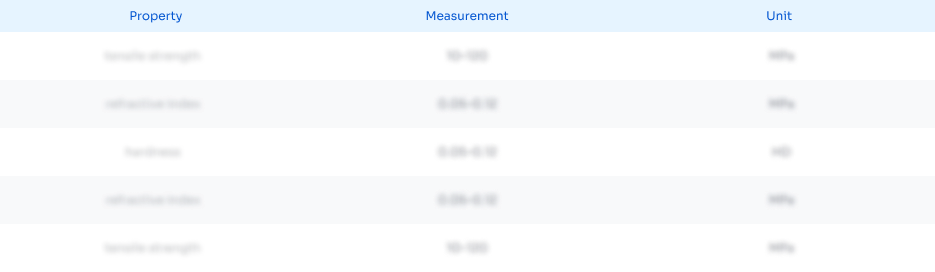
Abstract
Description
Claims
Application Information

- Generate Ideas
- Intellectual Property
- Life Sciences
- Materials
- Tech Scout
- Unparalleled Data Quality
- Higher Quality Content
- 60% Fewer Hallucinations
Browse by: Latest US Patents, China's latest patents, Technical Efficacy Thesaurus, Application Domain, Technology Topic, Popular Technical Reports.
© 2025 PatSnap. All rights reserved.Legal|Privacy policy|Modern Slavery Act Transparency Statement|Sitemap|About US| Contact US: help@patsnap.com