A kind of solid organic dehydrating agent and preparation method thereof
A dehydrating agent and organic technology, applied in the field of solid organic dehydrating agent and its preparation, can solve the problems of structural stability and poor water filtering effect, and achieve the effect of improving production efficiency
- Summary
- Abstract
- Description
- Claims
- Application Information
AI Technical Summary
Problems solved by technology
Method used
Image
Examples
Embodiment 1
[0038] Add 3740kg of deionized water to the batching kettle, start stirring, add 3710kg of 40% acrylamide aqueous solution, 10520kg of 80% acryloyloxyethyltrimethylammonium chloride monomer aqueous solution, UV monomer PETA0.15kg, 2kg Disodium ethylenediamine tetraacetate, 0.36kg sodium bisulfite; stir evenly to form a pre-polymerization liquid of a certain concentration, add citric acid to adjust the pH of the solution to about 4.00; The liquid is transferred to the oxygen removal device at 3 tons / hour for oxygen removal, and a macromolecular photoinitiator is added to the pipeline to polymerize [2-hydroxyl-2-methyl-1-[4-(1-methylvinyl)phenyl ]acetone] solution and azo initiator VA044 solution, concentration
[0039] Both are 10%, and the flow rate is 1.34kg / hour and 0.40kg / hour respectively. After mixing evenly, enter the ultraviolet light belt type equipment to carry out light-induced polymerization reaction. After the reaction is completed, the liquid becomes a rubber bloc...
Embodiment 2
[0041]Add 3740kg of deionized water to the batching kettle, start stirring, add 3710kg of 40% acrylamide aqueous solution, 10520kg of 80% methacryloyloxyethyltrimethylammonium chloride monomer aqueous solution, UV monomer PETA0.15kg, 2kg disodium ethylenediaminetetraacetic acid, 0.45kg sodium bisulfite; stir evenly to form a pre-polymerization liquid of a certain concentration, add citric acid to adjust the pH of the solution to about 4.00; turn on the cooling, reduce the material to 0 °C; The polymerization liquid is transferred to the oxygen removal device at 3 tons / hour for oxygen removal, and a macromolecular photoinitiator is added to the pipeline to polymerize [2-hydroxyl-2-methyl-1-[4-(1-methylvinyl)benzene Base] acetone] solution and azo initiator VA044 solution, the concentration is 10%, the flow rate is 1.34kg / hour and 0.40kg / hour respectively, after mixing evenly, enter the ultraviolet light belt type equipment to carry out light-induced polymerization reaction, afte...
Embodiment 3
[0043] Add 4410kg of deionized water to the batching tank, start stirring, add 13500kg of 80% acryloyloxyethyltrimethylammonium chloride monomer aqueous solution, UV monomer PETA0.15kg, 2kg ethylenediaminetetraacetic acid disodium, 0.45kg sodium bisulfite; stir evenly to form a pre-polymerization liquid of a certain concentration, add citric acid to adjust the pH of the solution to about 4.50; Deoxygenation device for oxygen removal, macromolecular photoinitiator polymerization [2-hydroxyl-2-methyl-1-[4-(1-methylvinyl)phenyl] acetone] solution and azo initiated in the pipeline VA044 solution, the concentration is 10%, the flow rate is 1.34kg / hour and 0.40kg / hour respectively, after mixing evenly, it enters the ultraviolet light belt type equipment for light-induced polymerization reaction, after the reaction is completed, the liquid becomes a glue block, and then the glue The lumps are granulated, dried, ground, and sieved to obtain solid sludge dewatering products;
PUM
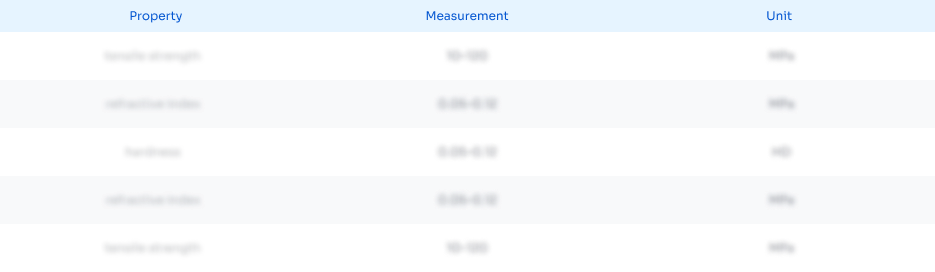
Abstract
Description
Claims
Application Information

- R&D
- Intellectual Property
- Life Sciences
- Materials
- Tech Scout
- Unparalleled Data Quality
- Higher Quality Content
- 60% Fewer Hallucinations
Browse by: Latest US Patents, China's latest patents, Technical Efficacy Thesaurus, Application Domain, Technology Topic, Popular Technical Reports.
© 2025 PatSnap. All rights reserved.Legal|Privacy policy|Modern Slavery Act Transparency Statement|Sitemap|About US| Contact US: help@patsnap.com