Compressor assembly process
An assembly process and compressor technology, which is applied in the field of compressors, can solve the problems of reducing the assembly accuracy requirements of compressor products, affecting the mass production of compressors, and increasing the operating noise of compressors, so as to ensure smoothness, stability and quality. Excellent effect of reducing compression leakage
- Summary
- Abstract
- Description
- Claims
- Application Information
AI Technical Summary
Problems solved by technology
Method used
Image
Examples
Embodiment Construction
[0045] see figure 1 and figure 2 The compressor assembly 1 includes a crankshaft 11, a machine base 13, three eccentric pins 18, a fixed base 17, a moving disk 16 and a static disk 14, the crankshaft 11 is rotatably supported on the machine base 13, and the moving disk 16 is mounted on a fixed On the seat 17, and the fixed seat 17 is sleeved on the crankshaft 11. Wherein, three eccentric pins 18 are evenly distributed in the circumferential direction of crankshaft 11, and the first end of each eccentric pin 18 is rotatably supported on the base 13, and the second end of each eccentric pin 18 is rotatably supported on a fixed On the base 17, a pressure plate 15 is fastened on the machine base 13 by a screw 117 and covered on the first end of an eccentric pin 18. Moreover, the static disc 14 cooperates with the movable disc 16 and is fixedly installed on the base 13 .
[0046] The assembly process of the compressor in this embodiment includes the assembly steps of the cranks...
PUM
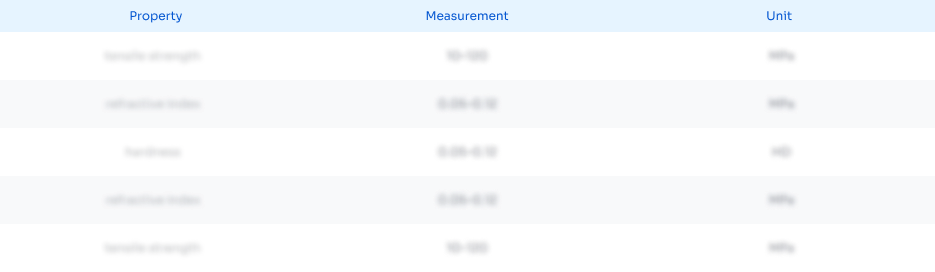
Abstract
Description
Claims
Application Information

- Generate Ideas
- Intellectual Property
- Life Sciences
- Materials
- Tech Scout
- Unparalleled Data Quality
- Higher Quality Content
- 60% Fewer Hallucinations
Browse by: Latest US Patents, China's latest patents, Technical Efficacy Thesaurus, Application Domain, Technology Topic, Popular Technical Reports.
© 2025 PatSnap. All rights reserved.Legal|Privacy policy|Modern Slavery Act Transparency Statement|Sitemap|About US| Contact US: help@patsnap.com