A method for automatic partitioning of shape features of aircraft structural parts
A technology of aircraft structural parts and shape features, applied in special data processing applications, geometric CAD, etc., can solve the problems of complex programming process, difficulty in ensuring efficiency and quality, and dependence on manual experience, so as to reduce the dependence on experience, improve efficiency and Quality, practical effect
- Summary
- Abstract
- Description
- Claims
- Application Information
AI Technical Summary
Problems solved by technology
Method used
Image
Examples
Embodiment Construction
[0072] The present invention will be further described below in conjunction with the accompanying drawings and embodiments.
[0073] An automatic zoning method for processing the shape features of aircraft structural parts, comprising the following steps: aiming at the shape features of aircraft structural parts, identifying all geometric surface attributes of the shape features according to the definition of geometric surface attributes, and establishing the association relationship between the shape geometric surfaces; Based on the principle of partitioning of the shape surface, the geometric surface of the shape feature is initially partitioned; then the position and shape information of the interference objects such as the part process boss and the pressure plate are obtained, and the positional relationship between the interference object and the shape geometric surface is established; finally, the initial shape processing is carried out according to the position of the int...
PUM
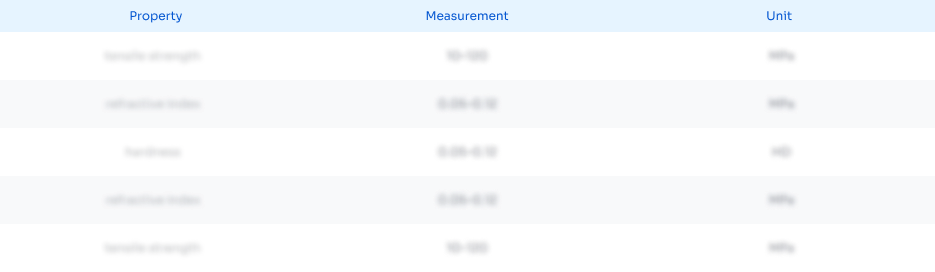
Abstract
Description
Claims
Application Information

- R&D
- Intellectual Property
- Life Sciences
- Materials
- Tech Scout
- Unparalleled Data Quality
- Higher Quality Content
- 60% Fewer Hallucinations
Browse by: Latest US Patents, China's latest patents, Technical Efficacy Thesaurus, Application Domain, Technology Topic, Popular Technical Reports.
© 2025 PatSnap. All rights reserved.Legal|Privacy policy|Modern Slavery Act Transparency Statement|Sitemap|About US| Contact US: help@patsnap.com