Welding wire speed regulation control system
A control system and speed regulation technology, applied in the direction of manufacturing tools, welding equipment, welding accessories, etc., can solve the problems of insufficient technical solutions, affecting the welding effect, and not considering the actual transmission status of welding wire, etc.
- Summary
- Abstract
- Description
- Claims
- Application Information
AI Technical Summary
Problems solved by technology
Method used
Image
Examples
Embodiment approach
[0025] As an embodiment of the present invention, a No. 1 limit assembly 4 is provided on the bottom surface of the frame 1 below the wire reel 2, and the No. 1 limit assembly 4 includes a No. 1 lead screw 41, a No. 2 lead screw 42, No. 1 slide bar 43, support block 44 and No. 2 motor 7; the axial direction of described No. 1 leading screw 41, No. 2 leading screw 42 and No. 1 slide bar 43 is parallel to the axial direction of welding wire reel 2, and the axial direction of described No. 1 Leading screw 41 and No. 2 leading screw 42 are symmetrically distributed on the both sides of No. 1 slide bar 43; Described support block 44 is two, two support blocks are positioned at the two ends of No. 1 slide bar 43, one side of support block 44 Slidingly connected on the No. 1 slide bar 43, the other side is connected with the No. 1 lead screw 41 and the No. 2 lead screw 42 respectively. The controller controls the No. 2 motor 7 to drive the No. 1 lead screw 41 to rotate, and the No. 2 ...
PUM
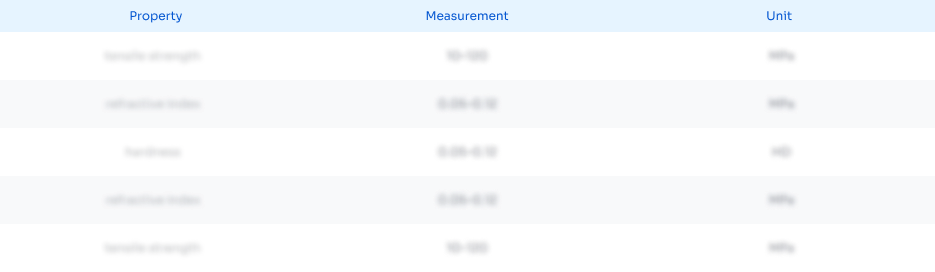
Abstract
Description
Claims
Application Information

- R&D Engineer
- R&D Manager
- IP Professional
- Industry Leading Data Capabilities
- Powerful AI technology
- Patent DNA Extraction
Browse by: Latest US Patents, China's latest patents, Technical Efficacy Thesaurus, Application Domain, Technology Topic, Popular Technical Reports.
© 2024 PatSnap. All rights reserved.Legal|Privacy policy|Modern Slavery Act Transparency Statement|Sitemap|About US| Contact US: help@patsnap.com