A three-degree-of-freedom pneumatic flexible actuator with variable stiffness and its preparation method
A flexible driver and driver technology, applied in manufacturing tools, program-controlled manipulators, cooling/ventilation/heating transformation, etc., can solve the problems of low response rate of stiffness adjustment and poor load-carrying capacity of the driver, and achieve low driving air pressure and enhanced thermal conductivity , the effect of improving stiffness
- Summary
- Abstract
- Description
- Claims
- Application Information
AI Technical Summary
Problems solved by technology
Method used
Image
Examples
Embodiment
[0033] Such as Figure 1 to Figure 3 As shown, a variable stiffness three-degree-of-freedom pneumatic flexible driver includes a driver body. One end of the driver body is provided with a mounting groove 1 arranged along its length direction, and a variable stiffness module 2 is embedded in the mounting groove. The variable stiffness module includes The liquid metal 3, the protective shell 4 and the heating element 5, the liquid metal is packaged inside the protective shell, several air cavities 6 are opened inside the driver body, the air cavities are arranged along the length direction of the driver body, and the gas pipe 7 inserted on the driver body One end of the air pipe communicates with the air cavity, and the other end of the air pipe extends to the outside of the driver body; the axis of the installation groove is arranged obliquely to the axis of the driver body, and the center of the opening end of the installation groove is on the axis of the driver body. The inst...
PUM
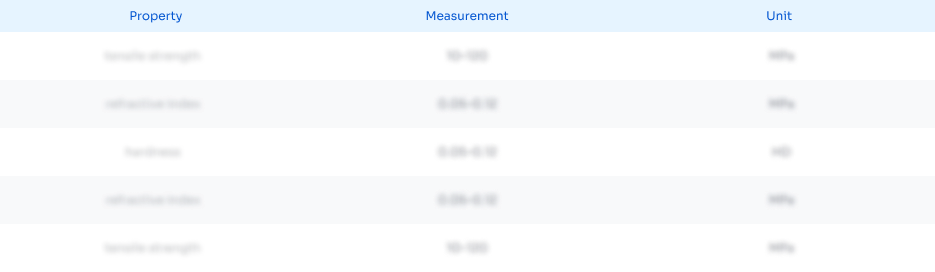
Abstract
Description
Claims
Application Information

- R&D Engineer
- R&D Manager
- IP Professional
- Industry Leading Data Capabilities
- Powerful AI technology
- Patent DNA Extraction
Browse by: Latest US Patents, China's latest patents, Technical Efficacy Thesaurus, Application Domain, Technology Topic, Popular Technical Reports.
© 2024 PatSnap. All rights reserved.Legal|Privacy policy|Modern Slavery Act Transparency Statement|Sitemap|About US| Contact US: help@patsnap.com