A control method for multi-mode vibration of a cable
A control method and multi-mode technology, which is applied in the field of multi-mode vibration control of cable-stayed bridge cables and vibration control of cable structures, can solve bridge installation difficulties, difficulties in installation and maintenance, and high-order vortex vibration control of cables Ineffective and other problems, to achieve efficient control, easy maintenance and replacement
- Summary
- Abstract
- Description
- Claims
- Application Information
AI Technical Summary
Problems solved by technology
Method used
Image
Examples
Embodiment Construction
[0031] The present invention will be further described below in conjunction with the embodiments shown in the accompanying drawings.
[0032] like figure 1 As shown, the present invention firstly provides a damper and TMD combined control method, which is optimized for the multi-mode vibration of the cable. First, the cable-damper-TMD system analysis model is established considering the sag effect, and the complex eigenfrequency equation of the system is obtained.
[0033] With sag cable-viscous damper-TMD system such as figure 2 shown. The cable is placed horizontally, the chord length is L, the horizontal tension is H, the mass per unit length is m, and the axial stiffness is EA. The damper has a damping coefficient of c and is installed at a distance l from the anchorage end of the left cable 1 location.
[0034] The stiffness, damping and mass of the TMD are denoted by k d 、c d 、m d means that ω d is the natural circular frequency of TMD, and ξ is the damping rat...
PUM
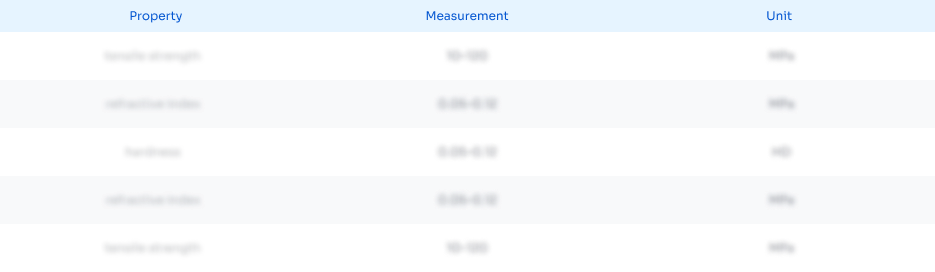
Abstract
Description
Claims
Application Information

- R&D
- Intellectual Property
- Life Sciences
- Materials
- Tech Scout
- Unparalleled Data Quality
- Higher Quality Content
- 60% Fewer Hallucinations
Browse by: Latest US Patents, China's latest patents, Technical Efficacy Thesaurus, Application Domain, Technology Topic, Popular Technical Reports.
© 2025 PatSnap. All rights reserved.Legal|Privacy policy|Modern Slavery Act Transparency Statement|Sitemap|About US| Contact US: help@patsnap.com