Orthogonal point laser double-measuring-head pose calibration test piece
A technology of pose calibration and dual probes, which is applied in the direction of measuring devices, optical devices, instruments, etc., can solve problems such as the inability to apply the measurement scene of the workpiece to be measured, the error of system accuracy, and the inability to reflect the calibration error of the origin of the probe.
- Summary
- Abstract
- Description
- Claims
- Application Information
AI Technical Summary
Problems solved by technology
Method used
Image
Examples
Embodiment Construction
[0015] Preferred embodiments of the present invention are described in detail below in conjunction with accompanying drawings;
[0016] An orthogonal-point laser double-probe pose calibration test piece is characterized in that it includes a clamping shaft section (I), a horizontal probe calibration shaft section (II), and a vertical probe calibration shaft section (III).
[0017] The clamping shaft section (I) is located at the end of the calibration test piece in the -Z direction, and the clamping shaft section (I) includes a positioning cylindrical surface (101) and a clamping prism surface (102); the axis of the positioning cylindrical surface (101) Coincident with the Z axis of the test piece coordinate system, the distance between its end surface and the XOY reference plane of the test piece coordinate system is a known fixed value; the clamping prism surface (102) is the suction surface where the calibration test piece is fixed on the detection device, and its The axis ...
PUM
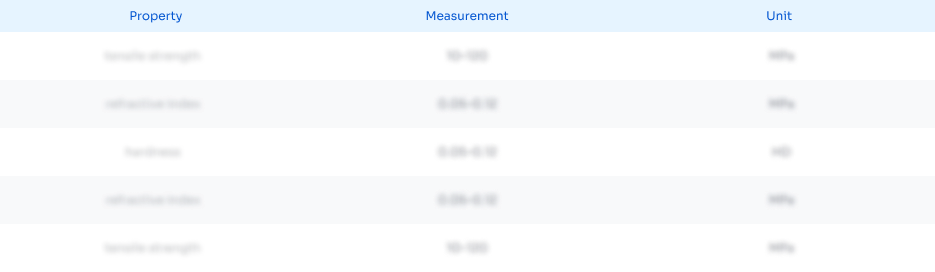
Abstract
Description
Claims
Application Information

- R&D
- Intellectual Property
- Life Sciences
- Materials
- Tech Scout
- Unparalleled Data Quality
- Higher Quality Content
- 60% Fewer Hallucinations
Browse by: Latest US Patents, China's latest patents, Technical Efficacy Thesaurus, Application Domain, Technology Topic, Popular Technical Reports.
© 2025 PatSnap. All rights reserved.Legal|Privacy policy|Modern Slavery Act Transparency Statement|Sitemap|About US| Contact US: help@patsnap.com