A lower leg mechanism and a biped robot equipped with the lower leg mechanism
A calf and ankle technology, applied in the field of biped robots, can solve the problems of large swing inertia, difficult control, heavy weight, etc., and achieve the effect of improving load carrying capacity, easy to be controlled, and high rigidity
- Summary
- Abstract
- Description
- Claims
- Application Information
AI Technical Summary
Problems solved by technology
Method used
Image
Examples
Embodiment 1
[0041] refer to figure 1 , this embodiment discloses a calf mechanism, including a calf frame 1, an integrated foot 2, an ankle support assembly 3 and two sets of ankle drive assemblies 4. The calf frame 1 and the integrated foot 2 are universally articulated through the above-mentioned ankle support assembly 3, and the ankle The drive assembly 4 is used to drive the integrated foot 2 to rotate around the ankle support assembly 3 .
[0042] refer to figure 2 , the integrated foot 2 has good shock absorption capability and can adapt to complex terrain. It includes a sole 21, a shock pad 22 bonded to the underside of the sole 21, and a support seat 23 arranged above the sole 21. The upper middle of the sole 21 A first connecting cylinder 24 is welded, and a second connecting cylinder 25 is welded on the lower side of the support base 23 . A shock-absorbing spring 26 is also arranged in the first connecting cylinder 24. One end of the shock-absorbing spring 26 is fixedly conne...
Embodiment 2
[0056] This embodiment discloses a biped robot, including the lower leg mechanism in the first embodiment.
PUM
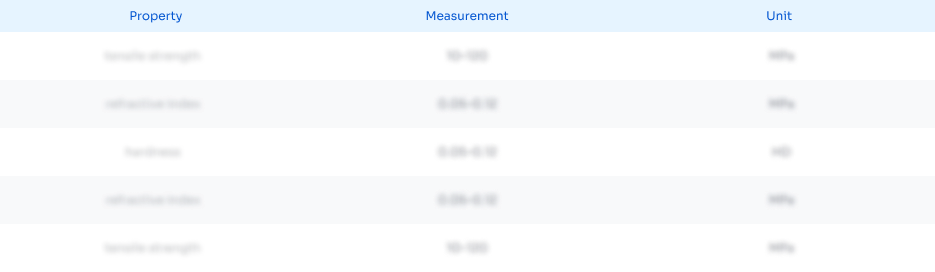
Abstract
Description
Claims
Application Information

- R&D Engineer
- R&D Manager
- IP Professional
- Industry Leading Data Capabilities
- Powerful AI technology
- Patent DNA Extraction
Browse by: Latest US Patents, China's latest patents, Technical Efficacy Thesaurus, Application Domain, Technology Topic, Popular Technical Reports.
© 2024 PatSnap. All rights reserved.Legal|Privacy policy|Modern Slavery Act Transparency Statement|Sitemap|About US| Contact US: help@patsnap.com