Automatic roll changing and continuous laminating equipment of flexographic printing machine
A flexo printing machine and lamination technology, applied in printing machines, general parts of printing machinery, printing, etc., can solve the problems of lower work efficiency, lower lamination efficiency, waste of equipment working time, etc., and achieve the effect of improving the degree of automation
- Summary
- Abstract
- Description
- Claims
- Application Information
AI Technical Summary
Problems solved by technology
Method used
Image
Examples
Embodiment 1
[0042] Such as Figure 1 to Figure 10 As shown, the present invention provides a flexo printing machine automatic roll-changing continuous film coating equipment, including:
[0043] A frame 1, the frame 1 is respectively provided with a coating part 2 and an automatic roll changing part 3;
[0044] The film covering part 2, the film covering part 2 includes a fixed plate 21 arranged symmetrically on the frame 1, a film covering assembly 22 arranged on the inner wall of the fixing plate 21, and a film covering assembly 22 located on the inner wall of the film covering assembly 22. One side and rotate the conveying roller 23 installed on the inner wall of the fixed plate 21;
[0045] The automatic roll change part 3, the automatic roll change part 3 is located on one side of the film covering assembly 22, and it includes a support frame 31 arranged on the frame 1, a mounting frame arranged on the support frame 31 32. The roller changing assembly 33 arranged on the side of the i...
PUM
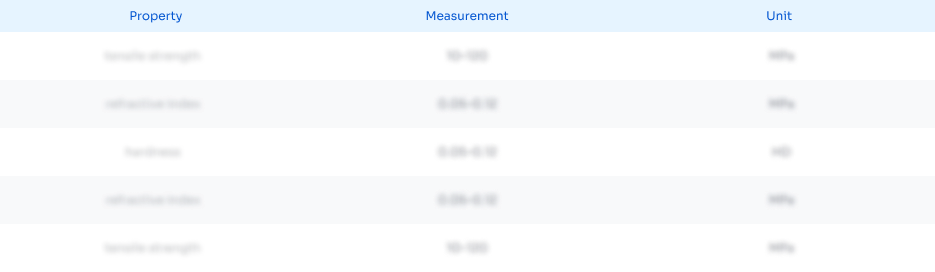
Abstract
Description
Claims
Application Information

- R&D Engineer
- R&D Manager
- IP Professional
- Industry Leading Data Capabilities
- Powerful AI technology
- Patent DNA Extraction
Browse by: Latest US Patents, China's latest patents, Technical Efficacy Thesaurus, Application Domain, Technology Topic, Popular Technical Reports.
© 2024 PatSnap. All rights reserved.Legal|Privacy policy|Modern Slavery Act Transparency Statement|Sitemap|About US| Contact US: help@patsnap.com