Milling fixture for automobile torsion bar moment arm thread end surface
A threaded end and torsion bar technology, which is applied in the field of milling processing of the threaded end face of the torsion bar arm used for turning over the automobile cab, can solve the problems of low machining accuracy and efficiency, high manufacturing cost, and irregular shape of the torsion bar arm , to achieve the effect of improving stability and accuracy
- Summary
- Abstract
- Description
- Claims
- Application Information
AI Technical Summary
Problems solved by technology
Method used
Image
Examples
Embodiment Construction
[0017] The following will clearly and completely describe the technical solutions in the embodiments of the present invention with reference to the accompanying drawings in the embodiments of the present invention. Obviously, the described embodiments are only some, not all, embodiments of the present invention.
[0018] In the present invention, terms such as "installation", "installation", "connection", "connection" and "fixation" should be interpreted in a broad sense, for example, it may be a fixed connection or It is a detachable connection; it may be a mechanical connection; it may be a direct connection or an indirect connection through an intermediary. Those of ordinary skill in the art can understand the specific meanings of the above terms in the present invention according to specific situations.
[0019] like Figure 1 to Figure 3 As shown, a milling fixture for the threaded end face of an automobile torsion bar arm includes: an upper base plate 1, a lower base pl...
PUM
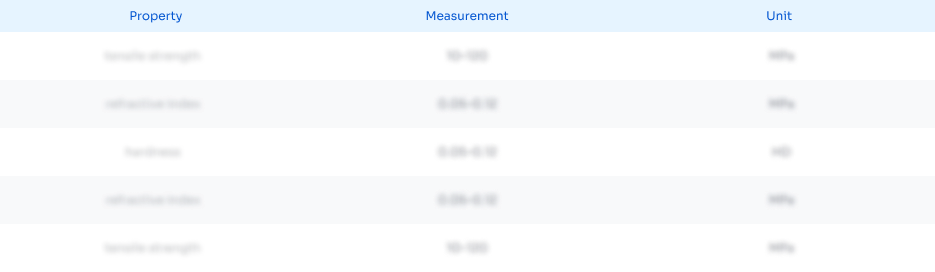
Abstract
Description
Claims
Application Information

- Generate Ideas
- Intellectual Property
- Life Sciences
- Materials
- Tech Scout
- Unparalleled Data Quality
- Higher Quality Content
- 60% Fewer Hallucinations
Browse by: Latest US Patents, China's latest patents, Technical Efficacy Thesaurus, Application Domain, Technology Topic, Popular Technical Reports.
© 2025 PatSnap. All rights reserved.Legal|Privacy policy|Modern Slavery Act Transparency Statement|Sitemap|About US| Contact US: help@patsnap.com