Adaptive holding current for electrically commutated electric motors
A technology of electric motor and current holding, applied in the deceleration device of DC motor, electronic commutation motor control, motor control and other directions, can solve problems such as adverse noise and electromagnetic radiation
- Summary
- Abstract
- Description
- Claims
- Application Information
AI Technical Summary
Problems solved by technology
Method used
Image
Examples
Embodiment Construction
[0054] Such as figure 1 As shown in , the control of a bipolar stepper motor 10 can be extended for adaptive hold-on. An adjustable holding current is fed by one of the two windings A or B, wherein the holding current is generated by at least one of the following methods:
[0055] - adjustable current source;
[0056] - Adjustable current sink;
[0057] - PWM-modulation with adjustable duty cycle; or,
[0058] - Chopper current control with adjustable current threshold.
[0059] A test current is modulated onto the second winding, the input energy of this test current being as low as possible, and the modulation of this test current is chosen to cause as little mechanical and acoustic disturbance as possible.
[0060] Common controls for bipolar stepper motors include final stages 12, 14, 16, and 18 connected to winding connections A0, A1, B1, B0, such as figure 1 shown in . figure 1 The structure of the final stage is shown as an example by means of the final stage 12 ....
PUM
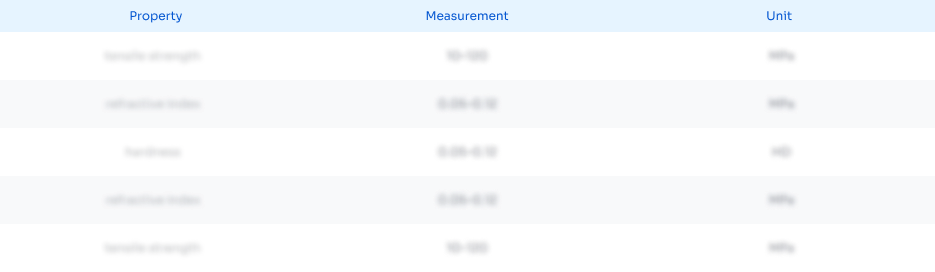
Abstract
Description
Claims
Application Information

- R&D Engineer
- R&D Manager
- IP Professional
- Industry Leading Data Capabilities
- Powerful AI technology
- Patent DNA Extraction
Browse by: Latest US Patents, China's latest patents, Technical Efficacy Thesaurus, Application Domain, Technology Topic, Popular Technical Reports.
© 2024 PatSnap. All rights reserved.Legal|Privacy policy|Modern Slavery Act Transparency Statement|Sitemap|About US| Contact US: help@patsnap.com