X-shaped, V-shaped and Y-shaped special-shaped component assembly method
A technology of special-shaped components and components, which is applied in the field of assembly of XVY-shaped special-shaped components, can solve problems such as difficulty in assembling special-shaped components, and achieve the effects of convenient splicing, reasonable force, and guaranteed quality
- Summary
- Abstract
- Description
- Claims
- Application Information
AI Technical Summary
Problems solved by technology
Method used
Image
Examples
Embodiment 1
[0023] Embodiment 1: XVY shape special-shaped member assembling method, comprises the following steps:
[0024] Step A: According to the results of measuring the position of the top surface of the installed components, judge the deviation value of the installed components, and then carry out the adaptability of the bottom connection surface of the special-shaped components (X-shaped, V-shaped or Y-shaped) to be installed Adjust machining (short stock and beveling) to compensate for deviations in installed components;
[0025] Step B: Use at least 3 length-adjustable slings to hoist the special-shaped component, and the hoisting points form at least a triangle; the sling is equipped with a chain block that can adjust the length of the sling; the lifting points are all close to the sides of the special-shaped component The edge of the outer contour increases the angle between the lifting ropes, which is conducive to increasing the stability of the special-shaped component after ...
Embodiment 2
[0031] The only difference from Implementation 1 is that in step B, an auxiliary positioning mechanism is set at the bottom of the special-shaped member 10 to be installed, such as figure 1 and figure 2 As shown, the auxiliary positioning mechanism includes a push rod 5, and a universal wheel 8 is installed on the lower end of the push rod 5; A connecting rod 13 is hinged between the supporting frame 11 and the lower supporting frame 12. A sleeve 6 is welded and fixed on the connecting rod 13. The sleeve 6 is slidably sleeved on the push rod 5. The sliding fit can realize the relative sliding between the ejector rod 5 and the support frame 1; the lower ends of the upper support frame 11 and the lower support frame 12 are all bolted to the positioning jack 7. A telescopic mechanism 3 is arranged between the middle part of the push rod 5 and the upper end of the upper support frame 11. The telescopic mechanism 3 includes a sleeve 32 and a movable rod 31. The movable rod 31 is...
PUM
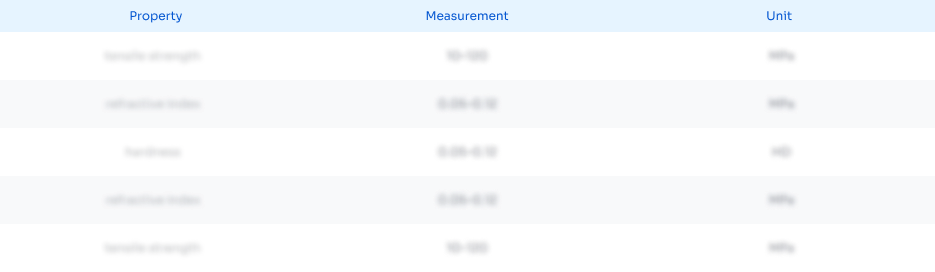
Abstract
Description
Claims
Application Information

- Generate Ideas
- Intellectual Property
- Life Sciences
- Materials
- Tech Scout
- Unparalleled Data Quality
- Higher Quality Content
- 60% Fewer Hallucinations
Browse by: Latest US Patents, China's latest patents, Technical Efficacy Thesaurus, Application Domain, Technology Topic, Popular Technical Reports.
© 2025 PatSnap. All rights reserved.Legal|Privacy policy|Modern Slavery Act Transparency Statement|Sitemap|About US| Contact US: help@patsnap.com