Sinusoidal swing welding method for welding robot
A welding robot and robot technology, applied in welding equipment, welding equipment, auxiliary welding equipment, etc., can solve the problems of low welding flexibility and poor welding effect, and achieve the effect of improving welding quality, improving welding effect and increasing rotation angle.
- Summary
- Abstract
- Description
- Claims
- Application Information
AI Technical Summary
Problems solved by technology
Method used
Image
Examples
Embodiment Construction
[0038] In order to make the purpose and technical solution of the present invention clearer, the technical solution of the present invention will be clearly and completely described below in conjunction with the embodiments of the present invention.
[0039] combine Figure 1-6 , the sine weaving welding method of the welding robot, the specific steps are as follows:
[0040] 1. Determine the reference plane of the swing:
[0041] First, determine the T of the current tool coordinate system according to the robot TCP point z Direction [0.688,-0.180,-0.702], then, T z The normal vector of the plane formed by the direction and the traveling direction of the current point of the weld track, and the plane formed by the traveling direction of the current point of the weld track are used as the reference plane of the swing. The specific method is as follows:
[0042] Take the travel direction of the current point of the weld trajectory as X w0 [0.688,-0.180,-0.702], the T of the ...
PUM
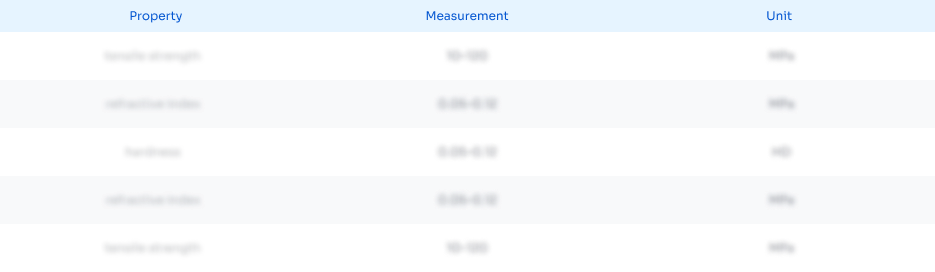
Abstract
Description
Claims
Application Information

- R&D
- Intellectual Property
- Life Sciences
- Materials
- Tech Scout
- Unparalleled Data Quality
- Higher Quality Content
- 60% Fewer Hallucinations
Browse by: Latest US Patents, China's latest patents, Technical Efficacy Thesaurus, Application Domain, Technology Topic, Popular Technical Reports.
© 2025 PatSnap. All rights reserved.Legal|Privacy policy|Modern Slavery Act Transparency Statement|Sitemap|About US| Contact US: help@patsnap.com