A bidirectional flying wing aircraft aerodynamic configuration and a design method
An aerodynamic shape and aircraft technology, applied in full-wing aircraft, aircraft parts, aircraft control and other directions, can solve the problems of insufficient control ability of rudder surface shape, and achieve the effect of solving the problem of insufficient control ability, simple design and easy realization.
- Summary
- Abstract
- Description
- Claims
- Application Information
AI Technical Summary
Problems solved by technology
Method used
Image
Examples
Embodiment 1
[0038] Embodiment 1, as figure 1 and figure 2 As shown, the present invention proposes an aerodynamic shape of a two-way flying wing aircraft, comprising a low-speed mode wing 1, a high-speed mode wing 8, a low-speed mode aileron 3, a high-speed mode aileron 6, and a low-speed mode elevator 2 , high-speed mode elevator 5, low-speed mode vertical tail 4 and high-speed mode vertical tail 7;
[0039] The high-speed mode wing 8 in the low-speed mode is the low-speed mode fuselage of the aircraft, the low-speed mode aileron 3 adopts the low-speed mode wing 1 without the high-speed mode elevator side wingtip as the full-motion control surface, and the low-speed mode elevator 2. The tail end of the low-speed mode fuselage is used as the rudder surface, and the low-speed mode vertical tail 4 is located on the symmetrical plane of the upper surface of the low-speed mode fuselage of the aircraft and before the low-speed mode elevator 2 .
[0040] The low-speed mode wing 1 in the high...
Embodiment 2
[0049] Embodiment 2, according to another aspect of the present invention, the present invention provides a kind of design method of aerodynamic profile of two-way flying-wing aircraft, and design method is as follows:
[0050] Determine the position of the low speed mode elevator, low speed mode aileron, high speed mode elevator and high speed mode aileron;
[0051] According to the longitudinal stability matching requirements of the aircraft in the low-speed mode and high-speed mode, the area of the elevator rudder surface in the low-speed mode and the elevator rudder surface area in the high-speed mode of the aircraft are respectively designed. Cause problems such as excessive hinge torque, the deflection angle of the elevator is constrained by the non-failure of the rudder surface, the area of the rudder surface of the low-speed mode elevator is 5% to 10% of the projected area of the whole machine, and the maximum available deflection angle of the rudder surface is -3...
PUM
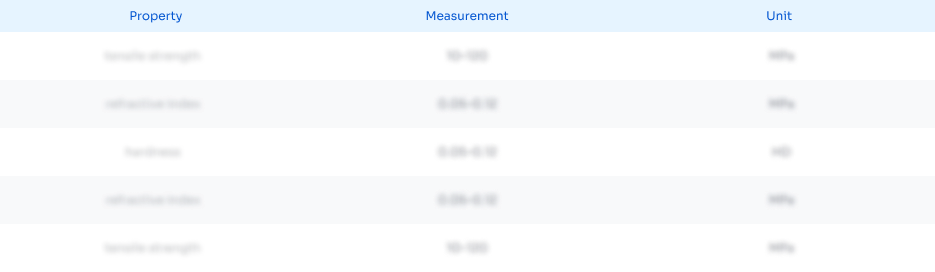
Abstract
Description
Claims
Application Information

- R&D Engineer
- R&D Manager
- IP Professional
- Industry Leading Data Capabilities
- Powerful AI technology
- Patent DNA Extraction
Browse by: Latest US Patents, China's latest patents, Technical Efficacy Thesaurus, Application Domain, Technology Topic, Popular Technical Reports.
© 2024 PatSnap. All rights reserved.Legal|Privacy policy|Modern Slavery Act Transparency Statement|Sitemap|About US| Contact US: help@patsnap.com