Material returning structure used for progressive die U-shaped sheet metal part, material returning method and application
A technology of sheet metal parts and U-shape, applied in the field of return structure of U-shaped sheet metal parts, can solve problems such as failure to meet normal supply of products, high production costs, and inconvenient return of materials, and achieve easy promotion, low cost, Facilitate the effect of process flow
- Summary
- Abstract
- Description
- Claims
- Application Information
AI Technical Summary
Problems solved by technology
Method used
Image
Examples
Embodiment Construction
[0024] In order to make the object, technical solution and advantages of the present invention more clear, the present invention will be further described in detail below in conjunction with the examples. It should be understood that the specific embodiments described here are only used to explain the present invention, not to limit the present invention.
[0025] In order to enable the U-shaped sheet metal parts to be returned smoothly on the progressive die, the invention discloses a material return structure for the U-shaped sheet metal parts of the progressive die, including a lower mold base 1, the lower mold base 1 is provided with a detachable drive core 2, and the left and right sides of the drive core 2 are respectively provided with a side slider 3, and the side slide 3 can slide up and down along the outside of the drive core 2; specifically Yes, the side slider 3 includes an integrally formed inclined part 3-1 and a horizontal part 3-2; the inclined part 3-1 is use...
PUM
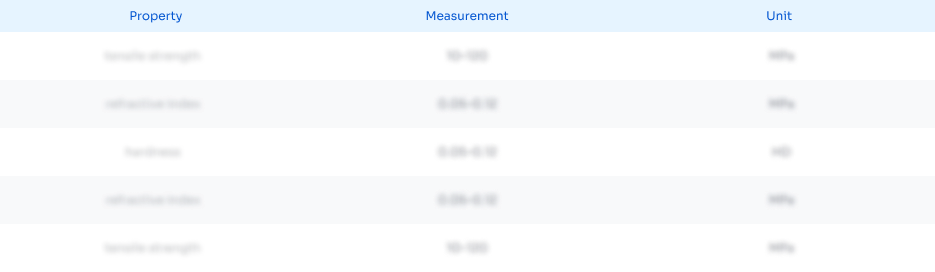
Abstract
Description
Claims
Application Information

- R&D Engineer
- R&D Manager
- IP Professional
- Industry Leading Data Capabilities
- Powerful AI technology
- Patent DNA Extraction
Browse by: Latest US Patents, China's latest patents, Technical Efficacy Thesaurus, Application Domain, Technology Topic, Popular Technical Reports.
© 2024 PatSnap. All rights reserved.Legal|Privacy policy|Modern Slavery Act Transparency Statement|Sitemap|About US| Contact US: help@patsnap.com