Automatic parameter calibration method and system
A parameter calibration and automatic technology, applied in the field of parameter calibration, can solve problems such as threshold or parameter differences, manual testing and modification troubles, etc., to achieve the effects of enhancing stability, reducing risks, and avoiding errors and errors
- Summary
- Abstract
- Description
- Claims
- Application Information
AI Technical Summary
Problems solved by technology
Method used
Image
Examples
Embodiment approach 1
[0048] refer to figure 1 , the automatic parameter calibration method provided by the present invention includes: placing the sweeping robot at a designated position, the designated position is set relative to the distance measuring device, the distance measuring sensor of the sweeping robot is facing the distance measuring baffle of the distance measuring device, the method includes step:
[0049] receiving the real distance between the distance measuring sensor and the distance measuring baffle sent by the distance measuring device, and acquiring the measured distance between the distance measuring sensor and the distance measuring baffle measured by the distance measuring sensor;
[0050] Calibrate the parameters of the ranging sensor according to the real distance and the measured distance.
[0051] The ranging sensor referred to in this embodiment can be any sensor that can measure or locate distance or position, including and not limited to infrared, ultrasonic, and las...
Embodiment approach 2
[0060] Such as figure 2 As shown, compared with Embodiment 1, an embodiment of the automatic parameter calibration method provided by the present invention adopts a distance measuring baffle to set multiple real distances, and calibrates the distance measuring sensor according to the real distance and the measured distance After the parameter step also include:
[0061] S30, adjusting the relative position of the distance measuring baffle of the distance measuring device and the sensor multiple times, and obtaining the real distance and the measurement distance between the distance measuring baffle and the sensor after each adjustment respectively;
[0062] S40, acquiring parameters of a plurality of ranging sensors according to the real distance and the measured distance acquired by each adjustment;
[0063] S50. Perform average calculation on the parameters of the plurality of ranging sensors to obtain final parameters of the ranging sensors.
[0064] The average calculat...
Embodiment approach 3
[0069] An embodiment (not shown) of the automatic parameter calibration method provided by the present invention is compared with Embodiments 1 and 2. The sweeping robot includes a plurality of distance measuring sensors, and each distance measuring sensor is correspondingly provided with one distance measuring sensor. A device for calibrating the parameters of a plurality of distance measuring sensors sequentially or simultaneously.
[0070] In this embodiment, multiple distance measuring sensors can be used step by step or simultaneously to measure, calibrate, and calculate multiple real distances, and the optimal calibration of parameters can be completed in a centralized and systematic manner, avoiding the problem of only a few sensors at a small number of predetermined distances. It has an optimal working environment, so that all sensors can operate under the working environment of the best parameters, and the accuracy, accuracy and sensitivity are improved.
[0071] In s...
PUM
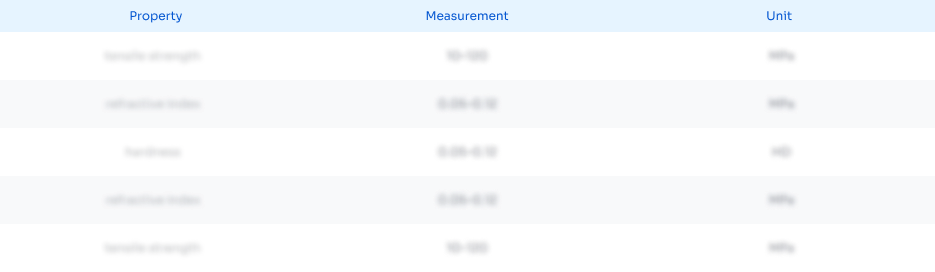
Abstract
Description
Claims
Application Information

- R&D
- Intellectual Property
- Life Sciences
- Materials
- Tech Scout
- Unparalleled Data Quality
- Higher Quality Content
- 60% Fewer Hallucinations
Browse by: Latest US Patents, China's latest patents, Technical Efficacy Thesaurus, Application Domain, Technology Topic, Popular Technical Reports.
© 2025 PatSnap. All rights reserved.Legal|Privacy policy|Modern Slavery Act Transparency Statement|Sitemap|About US| Contact US: help@patsnap.com