A Distributed Drive Variable Stiffness Joint Assist Mechanism
A power-assisted mechanism and variable stiffness technology, which is applied in the direction of manipulators, program-controlled manipulators, and manufacturing tools, can solve the problems of limiting the wide range of application environments, not being able to apply to popular people, and high equipment costs, achieving simple structure, precise joint drive, The effect of portable equipment
- Summary
- Abstract
- Description
- Claims
- Application Information
AI Technical Summary
Problems solved by technology
Method used
Image
Examples
Embodiment approach 1
[0028] figure 1 It shows the front sectional view of the joint booster mechanism. In the distributed drive variable stiffness joint booster mechanism, the elastic breathable fabric includes: elastic breathable fabric inner layer 1, elastic breathable fabric outer layer 2, and the hinge layer includes: the first hinge layer 5. The second hinge layer 6, the third hinge layer 9, the fourth hinge layer 10, the covering layer includes: the first covering layer 4, the second covering layer 7, the third covering layer 8, the fourth covering layer 11, the heating device It includes a first heating wire 13 and a second heating wire 14 . like figure 1 As shown, the first heating wire 13 and the second heating wire 14 cover the upper and lower surfaces of the shape memory polymer 3, and the first hinge layer 5, the second hinge layer 6, the third hinge layer 9, and the fourth hinge layer 10 are passed through DuPont Pyralux LF0100LF acrylic adhesive sticks it on the upper and lower sur...
PUM
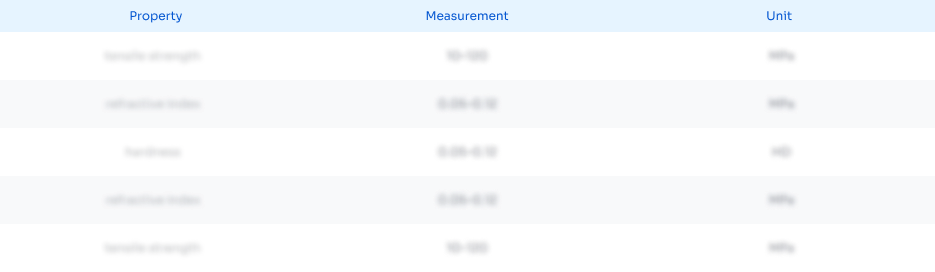
Abstract
Description
Claims
Application Information

- R&D Engineer
- R&D Manager
- IP Professional
- Industry Leading Data Capabilities
- Powerful AI technology
- Patent DNA Extraction
Browse by: Latest US Patents, China's latest patents, Technical Efficacy Thesaurus, Application Domain, Technology Topic, Popular Technical Reports.
© 2024 PatSnap. All rights reserved.Legal|Privacy policy|Modern Slavery Act Transparency Statement|Sitemap|About US| Contact US: help@patsnap.com