Wire insulation layer and preparation method thereof
An insulating layer and wire technology, applied in the field of wire insulating layer and its preparation, can solve the problems of wire insulation material performance change, poor wear resistance and aging resistance, and easy embrittlement after long-term use, and achieve excellent antibacterial effect. Effects of extended service life, excellent aging resistance and mechanical properties
- Summary
- Abstract
- Description
- Claims
- Application Information
AI Technical Summary
Problems solved by technology
Method used
Examples
Embodiment 1
[0022] An electric wire insulation layer, comprising the following raw materials in parts by weight: 29 parts of epoxy resin, 18 parts of polyvinyl chloride, 24 parts of ethylene-propylene rubber, 12 parts of glycerin solution, 20 parts of plant extract, 24 parts of modified bentonite, 16 parts of carbon black, 8 parts of aluminum hydroxide, 17 parts of zinc oxide, 18 parts of ethyl salicylate, 6 parts of stabilizer, 8 parts of antioxidant, 14 parts of curing agent, 12 parts of additives and 18 parts of coupling agent .
[0023] A preparation method for an electric wire insulation layer, comprising the following preparation steps:
[0024] a. Mix epoxy resin, ethylene propylene rubber, carbon black and antioxidant into the reaction kettle, heat and stir at 220°C for 30 minutes, then cool down to 150°C, continue to stir and add polyvinyl chloride, react for 1 hour, and cool to After normal temperature, material 1 was obtained;
[0025] b. Mix modified bentonite, aluminum hydr...
Embodiment 2
[0033] An electric wire insulation layer, comprising the following raw materials in parts by weight: 27 parts of epoxy resin, 18 parts of polyvinyl chloride, 22 parts of ethylene-propylene rubber, 15 parts of glycerol solution, 23 parts of plant extract, 18 parts of modified bentonite, 13 parts of carbon black, 14 parts of aluminum hydroxide, 12 parts of zinc oxide, 13 parts of ethyl salicylate, 7 parts of stabilizer, 9 parts of antioxidant, 11 parts of curing agent, 16 parts of additives and 18 parts of coupling agent .
[0034] A preparation method for an electric wire insulation layer, comprising the following preparation steps:
[0035] a. Mix epoxy resin, ethylene-propylene rubber, carbon black and antioxidants into the reaction kettle, heat and stir at 180°C for 30 minutes, then lower the temperature to 140°C, continue to stir and add polyvinyl chloride, react for 1 hour, and cool to After normal temperature, material 1 was obtained;
[0036] b. Mix modified bentonite,...
Embodiment 3
[0044] An electric wire insulation layer, comprising the following raw materials in parts by weight: 24 parts of epoxy resin, 22 parts of polyvinyl chloride, 20 parts of ethylene-propylene rubber, 15 parts of glycerin solution, 23 parts of plant extracts, 18 parts of modified bentonite, 13 parts of carbon black, 14 parts of aluminum hydroxide, 17 parts of zinc oxide, 13 parts of ethyl salicylate, 7 parts of stabilizer, 11 parts of antioxidant, 14 parts of curing agent, 14 parts of additives and 15 parts of coupling agent .
[0045] A preparation method for an electric wire insulation layer, comprising the following preparation steps:
[0046] a. Mix epoxy resin, ethylene-propylene rubber, carbon black and antioxidants into the reaction kettle, heat and stir at 220°C for 45 minutes, then cool down to 150°C, continue to stir and add polyvinyl chloride, react for 2 hours, and cool to After normal temperature, material 1 was obtained;
[0047] b. Mix modified bentonite, aluminum...
PUM
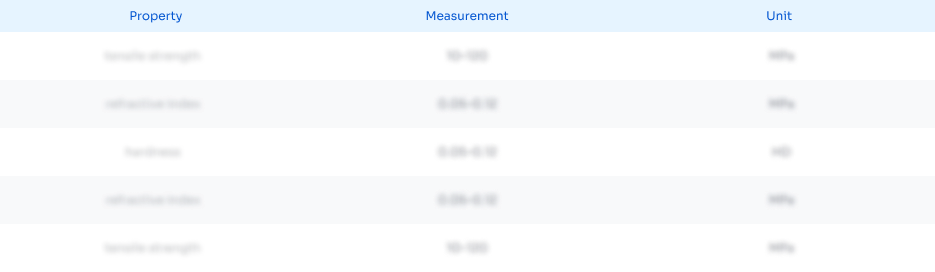
Abstract
Description
Claims
Application Information

- Generate Ideas
- Intellectual Property
- Life Sciences
- Materials
- Tech Scout
- Unparalleled Data Quality
- Higher Quality Content
- 60% Fewer Hallucinations
Browse by: Latest US Patents, China's latest patents, Technical Efficacy Thesaurus, Application Domain, Technology Topic, Popular Technical Reports.
© 2025 PatSnap. All rights reserved.Legal|Privacy policy|Modern Slavery Act Transparency Statement|Sitemap|About US| Contact US: help@patsnap.com